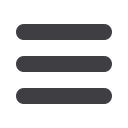
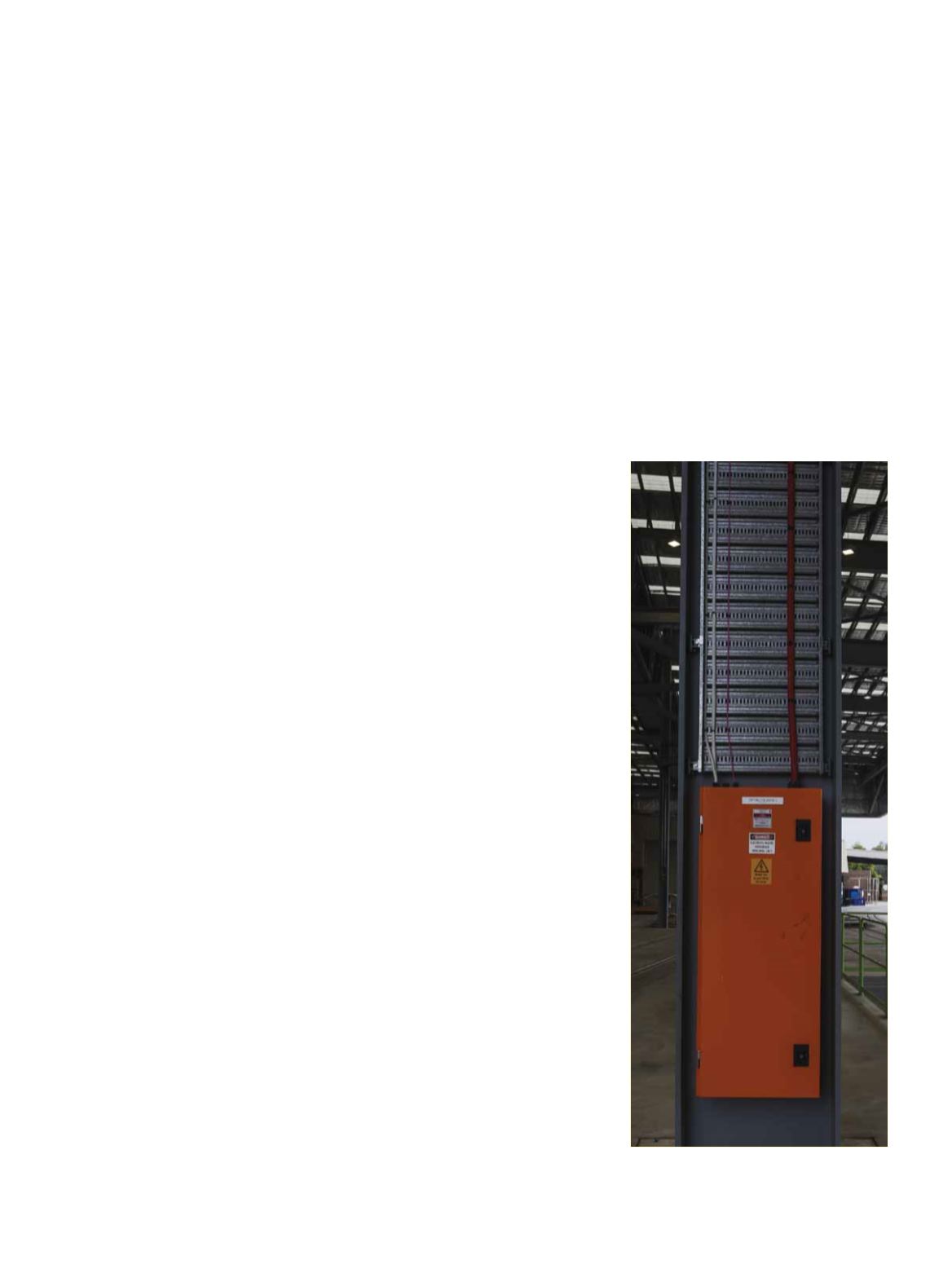
www. e l e c t r i c a l c o n n e c t i o n . c om . a u
45
for the duration of construction to
maintain the existing workshop’s
1,500A supply; the replacement of a
35-year-old main switch board with
a new 2,000A main switch board; as
well as the installation of a power
distribution system to feed four new
power busbar distribution rails, two
50T cranes, a 10T crane and 20 new
welding stations; along with all general
electrics for the workshops
new facilities.
A new lighting control system was
installed that incorporated day light
harvesting technology, to control
the lighting throughout the factory,
service trenches and carpark.
A new fibre link from the Telstra
network was installed to service the
expanding IT needs of Plasser. The
fibre link installation was staged
as the existing production facility
needed to maintain its services while
construction was under way.
Kerfoot also worked with the client
to design a new CCTV system to help
the client maintain a safe workplace
– vandalism and theft in the area is
quite high. A fibre link was installed
between buildings to maintain the
CCTV link, which was networked so it
could be monitored remotely.
A wireless fire smoke and EWIS
system was also installed, to cover the
new factory floor, integrated with the
existing factory’s system.
“Our goal was to complete the
project with no downtime. The careful
planning and dedication of the project
team helped us achieve this goal,”
project manager Josh Kerfoot says.
“As the support and cooperation of
the electrical and network authorities
were required to help with the staged
disconnection and installation of new
services, Kerfoot worked very closely
with them to design a connection
method that would comply with all of
their requirements and also meet the
critical milestone dates.
“Suppliers also had to be engaged
very early as many of the components
that were required had lead times
well over three months. Much of the
equipment was not your everyday
components and any late deliveries
would result in delays to the project.”
The Kerfoot team also worked with the
client to alter the sub-main requirements.
“There were several large sub-mains
that had to be installed in multiple
locations around the workshop.
We used flexible cabling, which is
commonly seen as being a more
expensive product. While this is
correct, with the right design input
we were able to reduce the size of the
sub-mains as the flexible cabling had
a larger current-carrying capacity,”
Josh says.
“It also allowed us to cut installation
time in half as flexible cabling is a lot
easier to install and terminate. The
cost benefit of this exercise was not
only for Kerfoot – it helped shorten the
installation time too which benefitted
the client and head contractor.”
Several of the electrical services
needed to be installed in the ground at
least two months before the building was
erected, Josh says.
“This posed a challenge as it was not a
simple trenching exercise,” he says.
“Internally and externally the building
contained hundreds of metres of rail
lines that required footings deep in the
ground. Further, the service trench and
wash down pit took up a lot of space,
which made it more challenging to find
appropriate places to run the cable.
“Kerfoot’s team worked with all of
the other trades involved in the project
to ensure all services were installed
in the exact location they needed to
be in, without affecting the building’s
structural elements.”
Once the building had been erected,
the installation of high-level services
would need to be carefully coordinated
as the use of lifting and access equipment
around the services trench, wash down
pit and rail track installation crews was
considered high risk.
“One of the most difficult aspects of the
project would be the installation of a
new substation and the decommissioning
of the old substation while keeping the
client operational.
“The existing substation was located
right in the middle of the new building’s
footprint and the construction schedule
did not allow time to have the factory built
Kerfoot had to install a new power supply
connection for Plasser Australia.