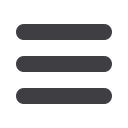
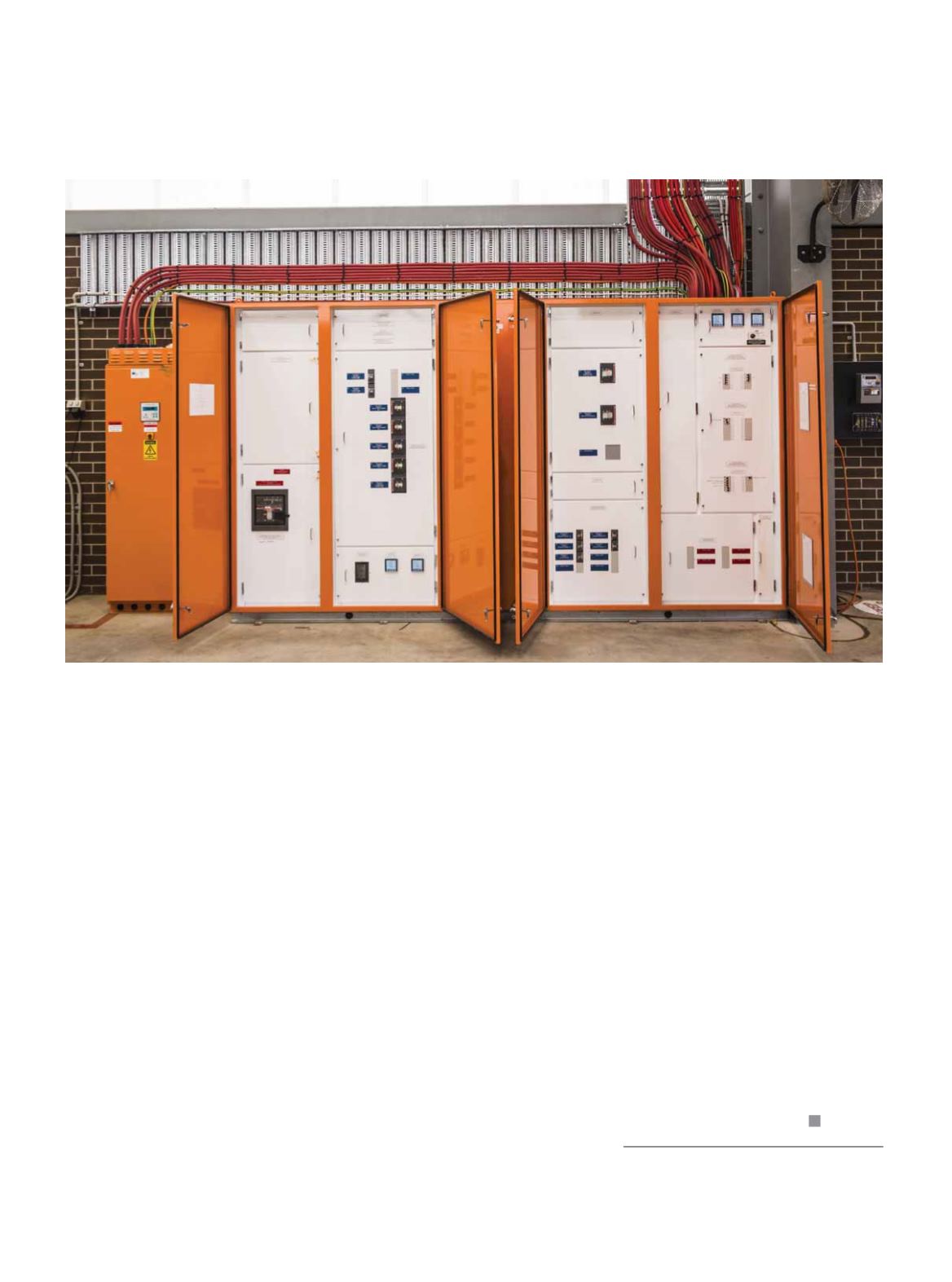
46 E L EC TR I C AL CONNEC T I ON
AU T UMN 20 1 7
and water tight before the old substation
could be removed.
“Kerfoot worked with the substation
installation team, the supply authorities
and the client to design a temporary
connection that would allow the removal
to the existing substation while ensuring
the facility would remain powered.
“This involved expediting the installation
of the new substation and the extension of
the client’s existing consumer mains so the
facilities could remain powered while we
waited for the newmain switch room to
be constructed.
Kerfoot designed a pit and conduit
network that would service both the new
main switch board and the temporary
connection so when it came time to feed
the newmain switch board there was
minimal down time.
“The temporary connection was simply
disconnected and the newmain switch
board connected. There was no waiting for
sub-mains to be installed and redirected as
this had already been done.”
Energy efficiency on this project was
a priority as the client’s running costs
were already very high. A lighting control
systemwas installed that used day light
harvesting, to allow the client to only
use lights within the factory and in the
undercover storage area when required.
“PE cells were installed within the factory
using the clear sections of roofing that had
been installed to let natural lighting in, this
saved a lot on money on installation cost as
the PE cells did not have to be installed on
the external facade of the bulling.
“The lighting control has been broken up
into groups so if one area is darker than
another it will turn on only the lighting in
this first area, stopping the use of lighting
when not required.
“Originally, the brief called for LED
high-bay lighting for the entire factory. But
the recommended brand’s fitting was not
only extremely expensive it was not very
serviceable either. It would accumulate a
lot of dust quite quickly.”
Kerfoot worked with a local supplier to
propose a fitting that would give the same
light output but half the cost, particularly
when it came to maintenance as the new
fitting was designed to collect minimal
amounts of dust.
A regular clean to help with the lights’
performance would not be required.
Most recently, Kerfoot’s work on the
Plasser facility won the NECA NSW
Excellence Award in the Industrial – Small
Project category.
“It just goes to show howwell our team
has adapted to innovation, safety and
code requirement changes and been able
to help the company grow constantly over
the last 40 years,” Josh says.
> Kerfoot
www.kerfootelectrics.com.auSeveral of the electrical services needed to be installed in the ground at least two months before the building was erected.