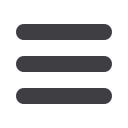
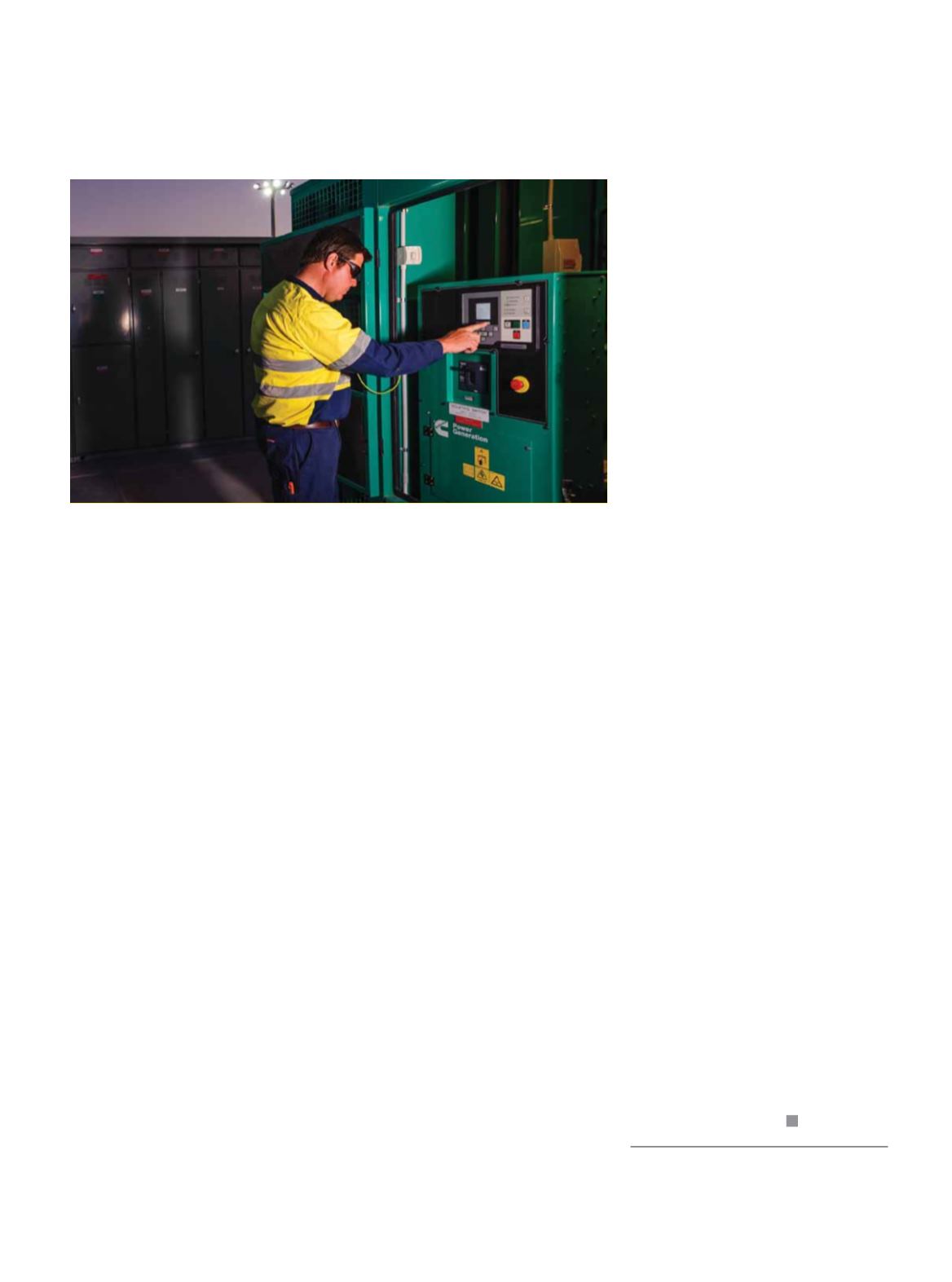
www. e l e c t r i c a l c o n n e c t i o n . c om . a u
51
on a reduced scope were also unable to
bring the project’s overall costs within
the required budget and would inhibit the
projects approval.
“Gordon McKay was then approached
by Racing Victoria to review the proposed
scope and make recommendations that
would help reduce the project’s overall
costs. Calling upon our past experience
with the racing industry and applying
innovative thinking on how the race
course was to be operated, Gordon McKay
was able to provide an alternative to
the base offer that reduced the overall
projected cost by around 40% while
having no effect on the final result.”
This was achieved by:
>
Altering minor cosmetic details, such as
changing the lighting mast structure to a
standard 16-side mast;
>
Decentralisation of the power compound
from one large, centrally-located
compound to two smaller compounds
located at each end of the race course.
This reduced the cost of the generators
and greatly reduced the length and size
of cabling to be installed; and,
>
Providing local control panels, which
allowed changing fromAstroturf to a real
grass surface at each mast and reduced
the requirement to install individual
feeder cables.
Being awarded the project after
the 2016 racing season calendar was
published challenged Gordon McKay
with an extremely tight seven-month
construction period.
“The development of fork-mounted
cable stands allowed cable installation
to progress at a greatly increased rate
while reducing the risk of having exposed
trenches through the unpredictable
Victorian winter/spring weather, and
similarly reducing exposure to horses and
jockeys at race meetings and during daily
track use.”
In all, 56 lighting masts supporting 1,190
light fittings powered by four generators,
58 control panels and 150,000m of cable
was installed and fully commissioned
three weeks early.
“The two tracks are now illuminated
from 56 steel lighting masts ranging in
height from 12m to 40m, supporting
1,190 2kW floodlights which equals
2.38MW of lighting.
“4km of trenching and 150,000m of
electrical cable is powered by four diesel
generators capable of supplying 2.75MW.”
All of this is centrally controlled by
course officials.
The Gordon McKay team identify a
new device called the Active Reactor as a
major factor in getting this job completed
on budget and ahead of schedule.
Developed in Australia, the Active
Reactor was designed to enable the
efficient control and operation of high
intensity discharge (HID) lamps. The
device uses a microchip and electronics
to control the starting and running of
150W to 2,000W high pressure sodium
and metal halide lamps commonly used in
street lighting, floodlighting, industrial and
sports lighting.
It also delivers substantial energy
savings, greenhouse gas reductions
and lamp life extension when used with
HID lamps.
“The device, which incorporates a
dimming capability, allows track officials
full control over the lighting system via a
computer-based SCADA control system,
including the ability to dim the lights
to 60% of the design level before, in-
between and at the conclusion of races to
save energy.”
Unlike other construction sites, minor
details mattered a great deal in this
project. For example, a loose cable tie
or a scrap of insulation tape could spook
a horse with horrifying results. It was
important to constantly be reminded of
this fact.
As project manager Rob Morris put
it: “Faced with what seemed to be a
near impossible challenge created by
an extremely tight budget and tighter
construction period, confirmed that good
pre-project planning, innovative thinking
in how the works were to be executed
and the willingness of the client, suppliers
and subcontractors to fully collaborate
in a responsive and accessible manner
can transformwhat appears to be
unachievable into achievable with results
exceeding expectations.”
> Gordon McKay
www.gmckay.com.auGordon McKay proposed the decentralisation of the power compound from one large,
centrally-located compound to two smaller compounds at each end of the race course.