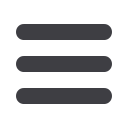
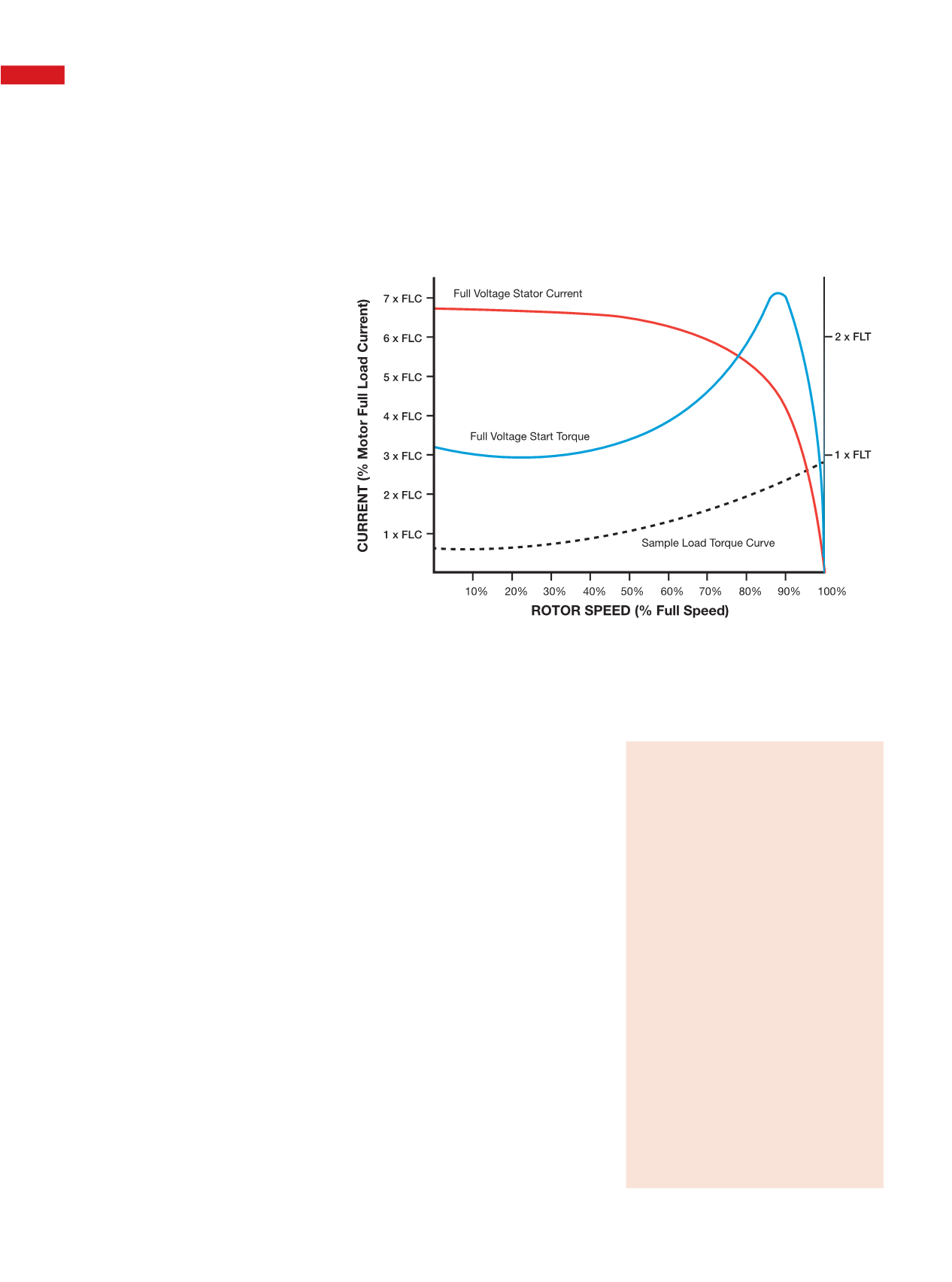
38 E L EC TR I C AL CONNEC T I ON
S PR I NG 20 1 6
ONLY FOOLS RUSH IN
H
igh-efficiency motors are
one contribution to saving
the planet.
Their use can save money
by reducing electrical energy
consumption per kilowatt of
mechanical power output.
Clever design has created motors in
which maximum energy is transferred
across the air gap between stator and
rotor (we are mainly concerned here
with induction motors).
Rotor electrical losses have been
reduced as far as possible; windage
and bearing losses have been shaved
to the nth degree.
This is obviously a great thing,
and many readers will be familiar
with Minimum Energy Performance
Standard (MEPS) requirements for
motors.
In Australia we are a little behind
Europe, where MEPS has been
replaced by ‘ie’ classifications. It
started there with ie1, then ie2, is
now ie3 and ie4 is about to happen.
With each new step efficiency has
been increased.
Of course, not all applications
demand the use of high efficiency
motors, but in the review of
requirements in Table 1, you’ll see that
most applications are captured in ie3.
The Standard is not enforced in
Australia; however, that is not very
important because most of our
motors are imported and can be
expected to accord with the higher
efficiency of ie3.
So why devote an article to this? In
short, because some things have to be
taken into account for motor control.
The price paid for having a high-
efficiency motor is that it draws an
inconveniently high inrush current
compared with lower-efficiency units.
The tacit assumption is that motors
are started direct on line (DOL). So
we are talking about lower-rating
motors running at low voltage (LV)
distribution level.
It is not a rare application area,
and motors for a variety of tasks
from air compressors, injection-
moulding machines, bottling lines,
pallet wrapping, CNC machines, many
conveyor belts, etc, fall in into the 2kW
or more range, and perhaps as high
as 30kW.
When ie3 motors are employed in
DOL mode, for example, unless the
protection level is chosen wisely there
is a chance that the protective device
will be tripped on starting the motor.
(It is assumed that the rated current
THE TRIPPING OF HIGH-EFFICIENCY
MOTORS ON START-UP NEEDS
A BIT MORE THAN A SIMPLE
SOLUTION.
PHILKREVELD
EXPLAINS IT ALL.
Figure 1: Characteristics of a typical induction motor.
TABLE 1
The ie3 regulation affects all standard
applications for three-phase motors with
the following criteria:
>
two to six poles;
>
rated voltage up to 1,000V;
>
rated output power from 0.75kW to
375kW; and,
>
rated on the basis of continuous-duty
operation.
The following motors are not affected:
>
motors designed for multiple speeds;
>
motors that are completely integrated
into a machine (pumps, fans,
compressors);
>
motors with integrated frequency
converters (compact drives) if the motor
cannot be tested separately from the
converter;
>
brake motors if the brake is an integral
part of the internal design of the motor;
>
specially designed submersible motors;
and,
>
smoke extraction motors with a
temperature class above 400°C.
LET’S GET TECHNICAL