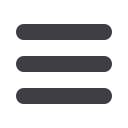
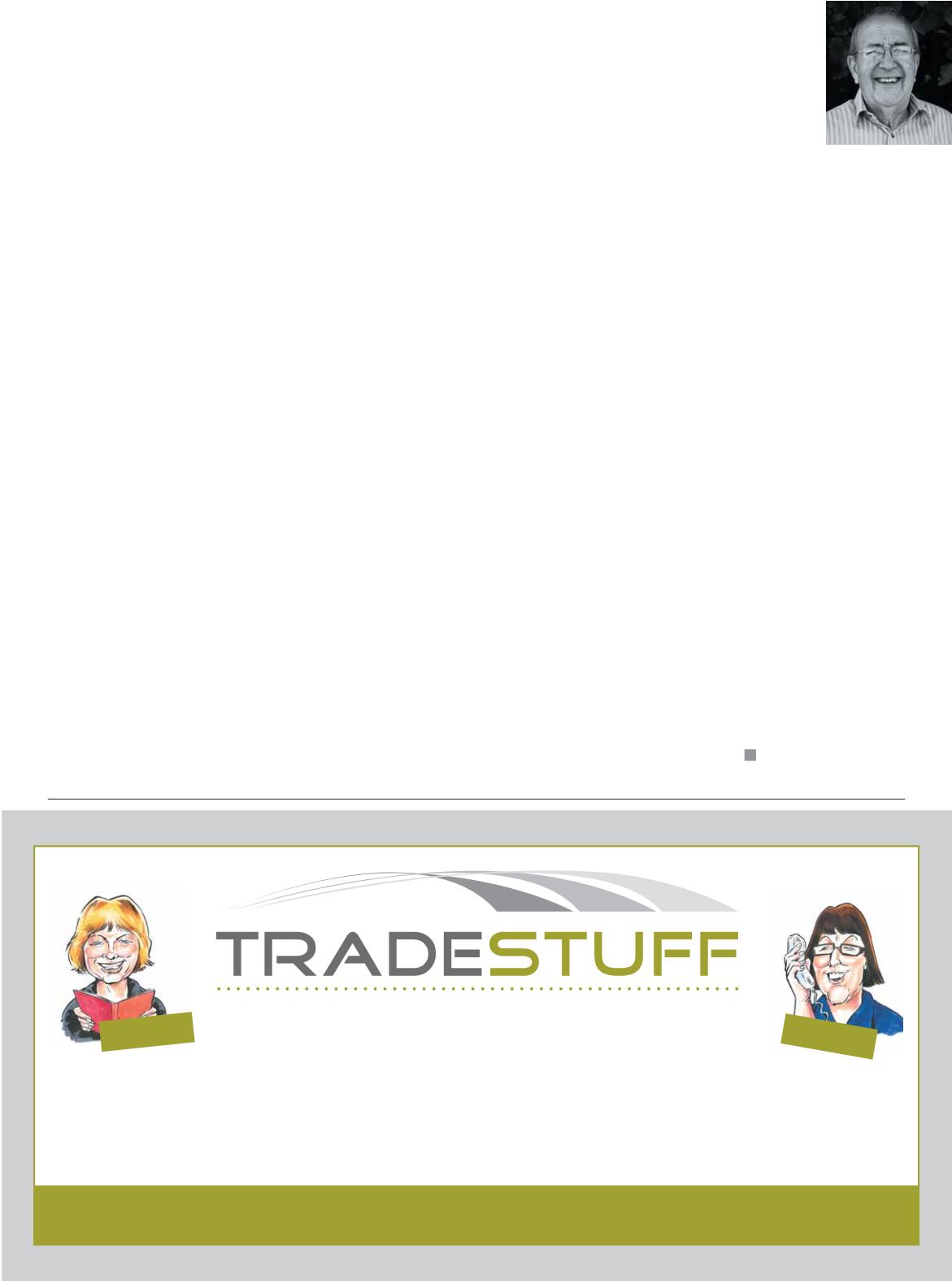
a u
3 7
with
Phil Kreveld
battens or purlins, but the leak-proofing
methods will vary.
Fixing to purlins is generally preferred,
but the installer needs to check the location
carefully before the installation date. Steel
roofs require fixing of panel hardware by
means of rubber pads, which provide leak
proofing and isolation.
The isolation aspect is important, as
nearly all solar systems have only a safety
ground. The functional ground is absent
in a transformer-less inverter installation,
but earth leakage current flows via the
capacitance panels have to ground
nevertheless. For a steel roof this can be
considerable.
Apart from the power considerations
that determine the number of panels, wind
conditions have to be taken into account. As
a rule of thumb, mounting panels close to
the edges of roofs should be avoided.
The Northern Territory, northern
Queensland and Western Australia
are subject to cyclonic conditions, so
installations must adhere to Australian
Standard (AS) 1170.2.
Although panels look like part of the roof,
they are separated from the roof surface
by an appreciable distance. Wind exposure
causes lift and drag forces on the panels
that increase as the square of wind velocity.
The higher the roof pitch and panel location
the more pronounced the effects. Sufficient
anchoring to the roof structure is crucial.
In planning roof fixtures, first look at the
location. (For simplicity’s sake a conventional
pitched roof is assumed.)
If the installation is in Brisbane (region B
of the Australian Standard) the anchoring
points for the solar panel fixtures will
increase. Brisbane is subject to higher wind
speeds than Melbourne and most of the
south coast (region A).
Next, the roof is divided into three equal
zones: a central zone and two end zones.
The end zones bordering the roof edge
are subject to higher wind speeds than the
centre, so the anchoring points and number
of rails will increase.
There must also be an exclusion zone so
that panels are not mounted right on the
roof edges.
The terrain categories must now
be considered. Open country without
windbreaks is the worst situation, compared
with built-up areas.
A combination of open or built-up
terrain and wind speed region determines
the number of anchoring points per rail.
Installers should consult their supplier for
appropriate engineering detail.
The ‘install and forget’ mentality that
marks much of the industry is not helpful,
because installations degrade over time.
The quality of roof-mounting materials
has quite a bearing on the effective lifespan
of the installation. The weather can promote
galvanic corrosion; dissimilar metals and
water being the ingredients. Oxidation can
halt corrosion – but don’t count on it.
Marine and industrial environments can
speed up corrosion. Sulphur dioxide and
nitrous oxides in industrial and heavy traffic
areas, and chlorides in seaside locations,
require precautions to be taken.
When in doubt, seek ways of physically and
electrically separating potentially problematic
metal combinations. Using rubber washers
to isolate galvanised screws from painted
steel sheet is common practice in the roofing
industry. Stainless steel washers with an
ethylene propylene diene monomer (EPDM)
gasket adhered are commonly available from
hardware suppliers.
GAIL
BRIGSY
DELIVERED DIRECT
TO YOUR DOOR
VISIT
WWW.TRADESTUFF.COM.AUAustralia’s largest resource of books, tools, and
standards for the electrical industry.