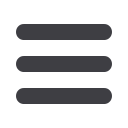

www. e l e c t r i c a l c o n n e c t i o n . c om . a u
63
BY
BRIAN
SEYMOUR
with computers in general and the
investment in equipment and training.
The ideal way of making the change
is to run parallel systems (manual and
electronic) to determine that the new
system reflects all the facts and themes
of the old one. However, this can be very
time consuming and not necessarily
attractive to management.
Contractors moving across to
electronic estimating need to start with
a simple spreadsheet program which
will make the calculations quickly and
accurately without too many ‘options’
to distract from the objective.
What does the estimator want
from an electronic program? Here are
the basics:
>
reliability and flexibility;
>
speed and accuracy;
>
technical support;
>
materials data base;
>
clearly defined segments;
>
individual segment pricing sheets, and
>
selling price assessment.
Many computer programs are
complete business management
systems, and estimating is only
one element.
It must be recognised that the
computer is only a tool. Although it
can make high-speed calculations, it
needs a thinking human to drive it. Even
the most expensive and sophisticated
programs cannot assess many of
the multiple variables that present
themselves in an electrical installation.
Competent trades people can make
a count and measure materials take-
off. Their dedication to quality will
determine the accuracy of quantities
entered in the estimate.
The count and measure is the
simplest part of the job. However, it
may be the largest proportion of the
task, and many thousands of dollars
may be represented by the following
variables – which can be assessed
only by an experienced and
competent person.
ENVIRONMENT
What concerns need to be tackled?
Here’s a list:
>
heat or cold (see below);
>
high-traffic areas, including vehicles
and pedestrians.
>
confined areas involving roof spaces,
duct risers, underfloor spaces,
switchboard cubicles and machinery;
>
dangerous conditions involving
high-voltage installations, hazardous
locations (chemical plants and
laboratories) and working at heights –
all adding to non-productive labour.
WALKINGTIME
The time taken to get from the site
shed or the parked vehicle to the work
area must be taken into account.
I have had projects with hundreds of
workers taking 10-20 minutes to walk
from the site sheds to the work area
every day for two or more years. This
can run into the hundreds of thousands
of dollars.
Even sole operators working in the
CBD and parking hundreds of metres
from the work area can rack up
considerable non-productive time.
They may have to carry tools,
equipment and materials to locations on
multiple floors.
TEMPERATURE
Working in extreme cold, such as
in refrigerated cool rooms or alpine
regions in winter will require a factor to
the labour allocation.
Working in the extreme heat
encountered in foundries, bakeries,
heating devices and roof spaces in
summer will need similar allowances.
WORKERSKILLS
Every facet of the industry has
specific skills.
Do all the workers on the site have the
skills to complete the installation within
the estimated time, or do they need
additional training and has this time and
cost been considered?
MATERIALSMOVEMENT
Getting materials to the work area is
another major concern.
Will vehicles be allowed on site? Is the
lifting free of charge or do you supply
your own? Is there free storage on site
or do you supply your own?
Can deliveries be made during normal
hours? Is there a restriction on the
quantity stored?
SITEACCESS
Is the job within the normal
travel allocation or is it outside the
award radius?
Does it require special transport to
deliver labour? Do all employees have to
pass through a security station?
The last point is not a great problem if
there are one or two employees, but it
can be extremely time consuming when
there are large teams on site.
Do all employees have to attend a job-
specific OH&S program? Do they all need
a specific licence to be allowed on site?
CONCLUSION
High-quality estimating software may
have some allocations built in, but none
can deal with all of the above variables
with any degree of confidence.
A well-trained and experienced
estimator is essential for appraising
the full extent of these ‘add-ons’ to
ensure all costs are included in the
tender submission.
Technology has enhanced productivity
considerably and has taken a great deal
of the drudgery out of estimating. It
has also allowed more flexibility when
applying ‘what if’ scenarios prior to
final submission.
If the data is not supplied by a
competent estimator, the final price
may be no more than a guesstimate.
Accounting for less-than-obvious
variables makes the difference between
disaster and a profit.