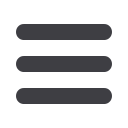
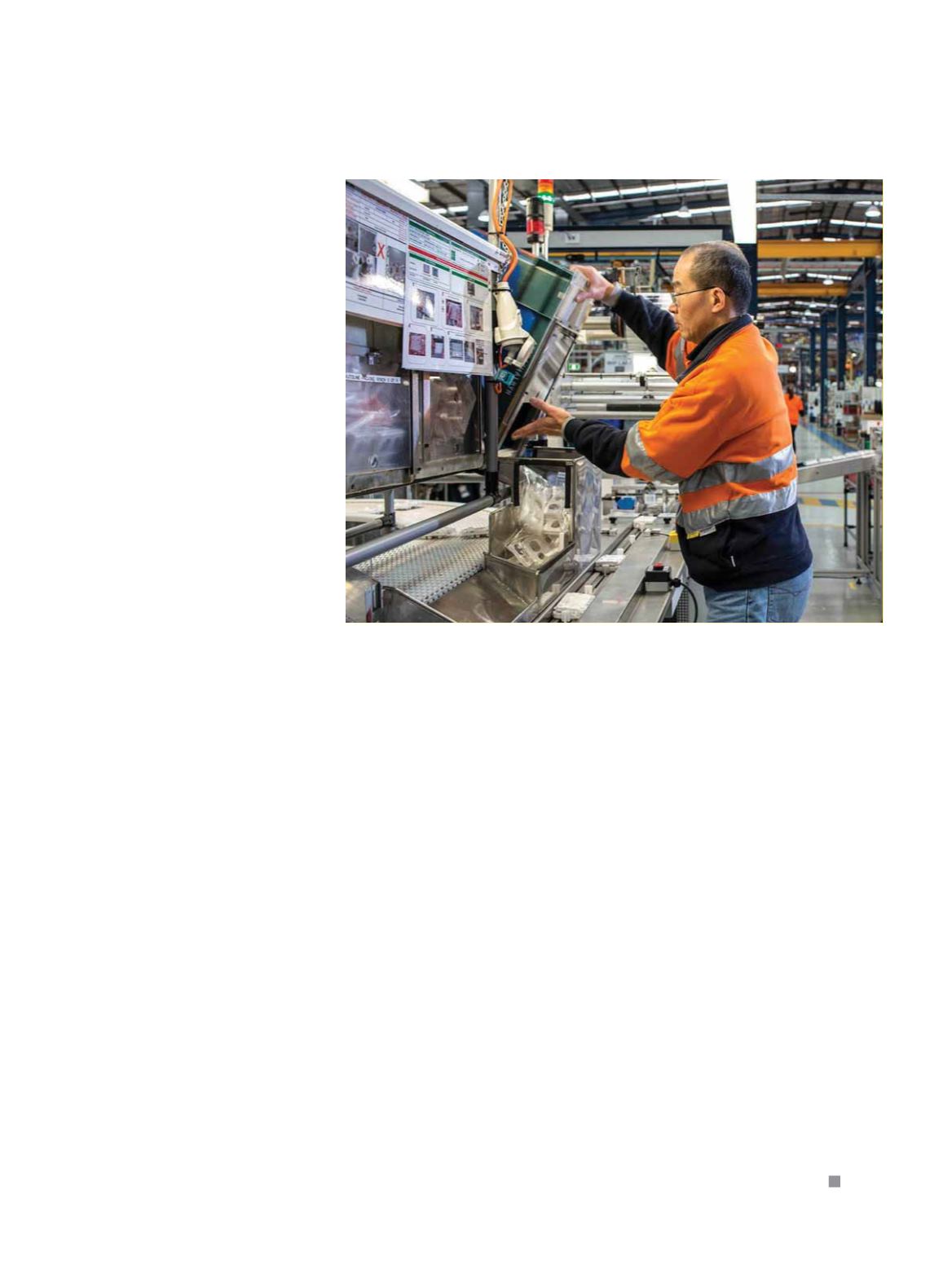
56 E L EC TR I C AL CONNEC T I ON
W I N T E R 20 1 6
the platform must be robust, scalable
and highly secure.
The platform then provides the
basis for the addition of any advanced
software applications that suit the unique
demands of a business. For example, in
a factory focused on food and beverage
production batch recipe management
software can be applied in settings as
diverse as cake baking to paint mixing.
This offers greater functionality for recipe
and process management, improving
material traceability and limiting cross
contamination. Energy management
software can also be integrated into the
platform to monitor and optimise the
use of energy across a plant. Effective
management of energy consuming
systems such as HVAC, lighting, and
blind control can reduce energy bills by
up to 30%.
WHERE ITHASWORKED
Vendors such as Schneider Electric
are at the heart of the global drive
to help industry design and build
smarter factories – and with it, improve
productivity, sustainability and efficiency.
The company recently worked with
F&N Dairies Thailand – a Food and
Beverage giant known for producing
popular canned milk and tea brands such
as Carnation, Teapot and Bear Brand – to
turn its production chain into a smarter
factory. Companies such as F&N are
continually faced with the challenge
to maintain high-quality products and
reduce waste, while at the same time,
keep operating costs to a minimum.
F&N produce three million cans of
milk a day so meeting quality control
standards across the production line
is no mean feat. In fact, when quality
parameter deviations were detected,
operators used to manually trace the
information in the archived, paper-based
operations sheets to determine the
root cause, which took up to four hours
per issue.
Today, with the development of a
new integrated platform and suite of
Wonderware software solutions from
Schneider Electric, F&N Dairies have now
optimised its entire enterprise, including
manufacturing execution, enterprise
integration, batch, quality, operations and
performance management.
And the result? The plant achieved its
production goal of 24 million cases, with
a full return on investment within one
year. It reduced quality traceability time
from four hours to just one minute. And
the plant achieved ‘100% First-Time
Quality’, a lean metric that indicates
what parts are manufactured correctly
the first time without need for inspection,
rework or replacement.
BEYONDTHE FUTURE
It is clear that the potential for smarter
working is limited only by our ability to
innovate applications. Advancements
in technology have provided the
connectivity, intelligence and automation
needed to drive productivity and quality,
while reducing cost and waste.
At its heart, the cyber-physical
revolution offers society the same
opportunity as industrial revolutions
gone by: the mindset and the tools
required to meet the challenges we
face today and beyond. Australian
companies can now embrace this change
and smart factories are the next step in
the journey to a fully connected and
more productive future.
While the role that electrical
contractors play in this space is still
evolving, what is certain is that the more
knowledge they have the better prepared
they can be for any outcome. Contractors
have the opportunity to understand how
factories will evolve, how this will change
the systems they currently work with and
where to up skill effectively to provide
the best service for their clients.
Cyber-physical revolution offers society the same opportunity as industrial revolutions
gone by: the mindset and the tools required to meet the challenges we face today.
and beyond.