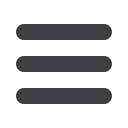
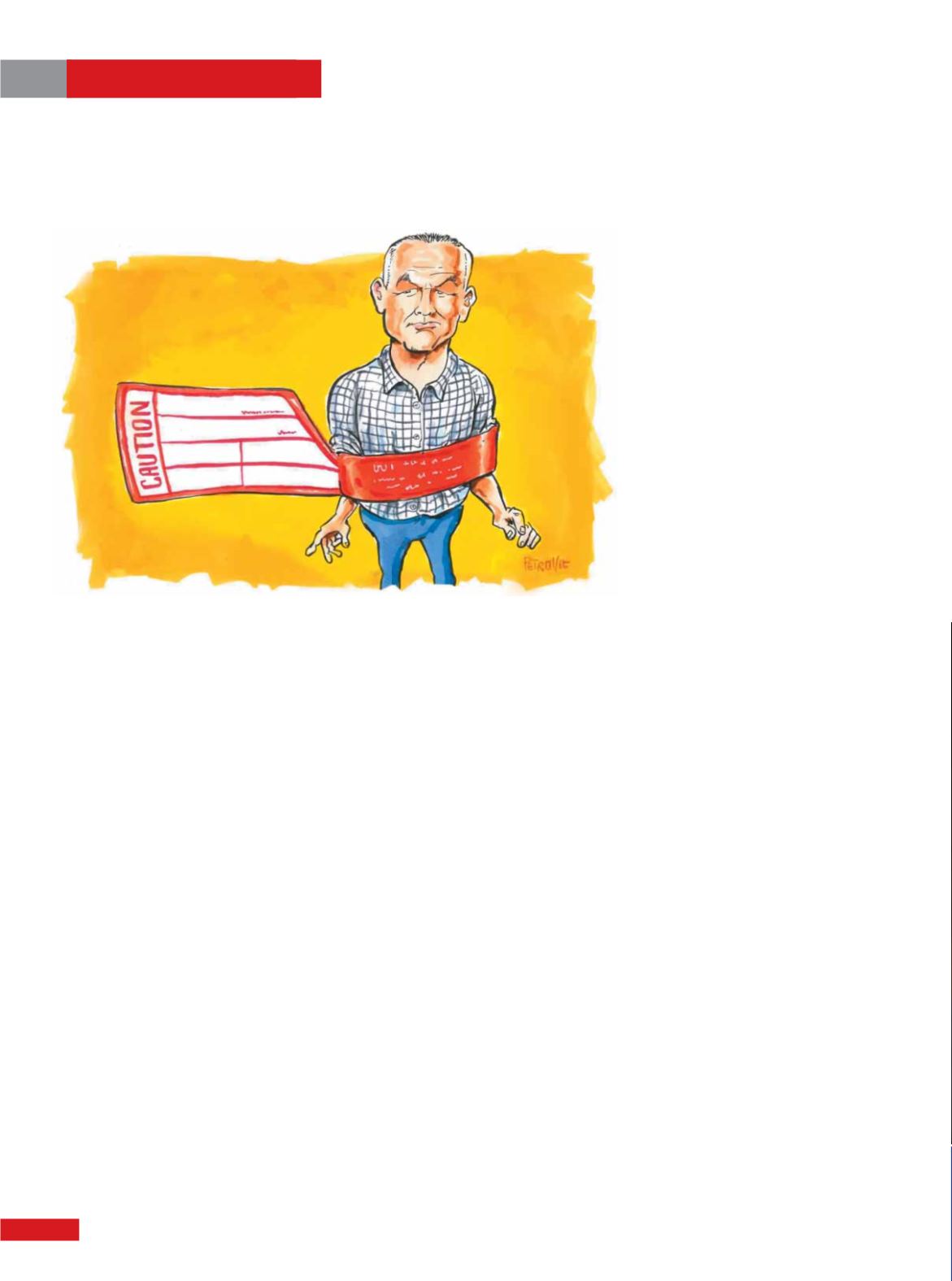
6 6
E L E CT R I C AL CONNE CT I ON
W I NT E R 2 01 5
TEST AND TAG
T
he owner of a small business that
had moved into new premises a
couple of years ago was keen to
reduce electricity consumption.
I was asked to carry out an energy audit,
during which I always look for obvious
safety issues or non-compliance with
electrical requirements. This distinguishes
me from energy consultants that have little
idea about electricity, and it adds value for
the client.
One constant issue is the testing and
tagging of electrical equipment, and most
of the gear at this business had none. A
couple of items had old tags from when
they were at the previous address, but only
one new appliance had a new tag – from
the supplier.
I always advise clients on Australian
Standards and legal requirements to help
them adopt safe practices for testing and
tagging. This time the client analysed what
I said instead of just accepting it.
The response was: “If we are not deemed
a hostile operating environment, why do we
do need to carry out testing and tagging?”
What a great question! Let’s investigate.
LEGAL REQUIREMENTS
The recently harmonised Work Health
and Safety (WHS) Regulation covers all
workplaces in Australia.
Section 150 states that electrical
equipment supplied by a socket outlet and
exposed to operating conditions likely to
result in damage or reduced life span must
be regularly inspected and tested.
Section 151 states that untested
equipment shouldn’t be used at a workplace
if it requires testing under Section 150.
Failure to comply attracts penalties
of $3,600 for individuals and $18,000 for
corporations.
Further, Section 165 requires that all
reasonable steps be taken to ensure regular
testing of residual current devices (RCDs)
for correct operation.
Keep in mind that RCDs do fail.
Some that we have tested lately don’t
trip, or are too slow to trip, and may not
save a life.
Looking at these sections in isolation,
one could conclude that testing and
tagging of electrical equipment is needed
only in hostile environments (perhaps
other than RCDs).
But how does a business demonstrate
its primary duty of care to workers and
other people? This duty is encapsulated in
Section 19 of the harmonised Work Health
and Safety Act.
If testing and tagging of electrical
equipment is not done or – as stipulated at
Section 21 that fixtures, fittings and plant be
without risk to personal health and safety –
the business cannot possibly fulfil that duty.
RELEVANT STANDARDS
AS/NZS 3760 is our normal ‘test and
tag’ Standard, but there are others likely to
impose additional requirements.
AS/NZS 3551 covers patient areas and
medical equipment, and AS/NZS 3012 deals
with construction and demolition sites, etc.
CODES OF PRACTICE
The Harmonised Code of Practice for
Managing Electrical Risks in the Workplace
2015
, requires a safe system of work
for the management of electrical
equipment (see Sections 3.1 and 3.2).
Section 3.2 does go on to say “not all
electrical items need to be inspected
and tagged under Regulation 150” and
“electrical equipment used in lower-risk
operating environments does not require
inspection and testing or tagging”.
However, it then goes on to discuss
the testing and tagging requirements of
AS/NZS 3760 for lower-risk environments.
Confused?
Testing and tagging of
electrical gear is now the norm
for businesses, but is it really
necessary?
Chris Halliday
of
PowerLogic investigates.
Testing times for electricians