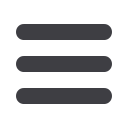
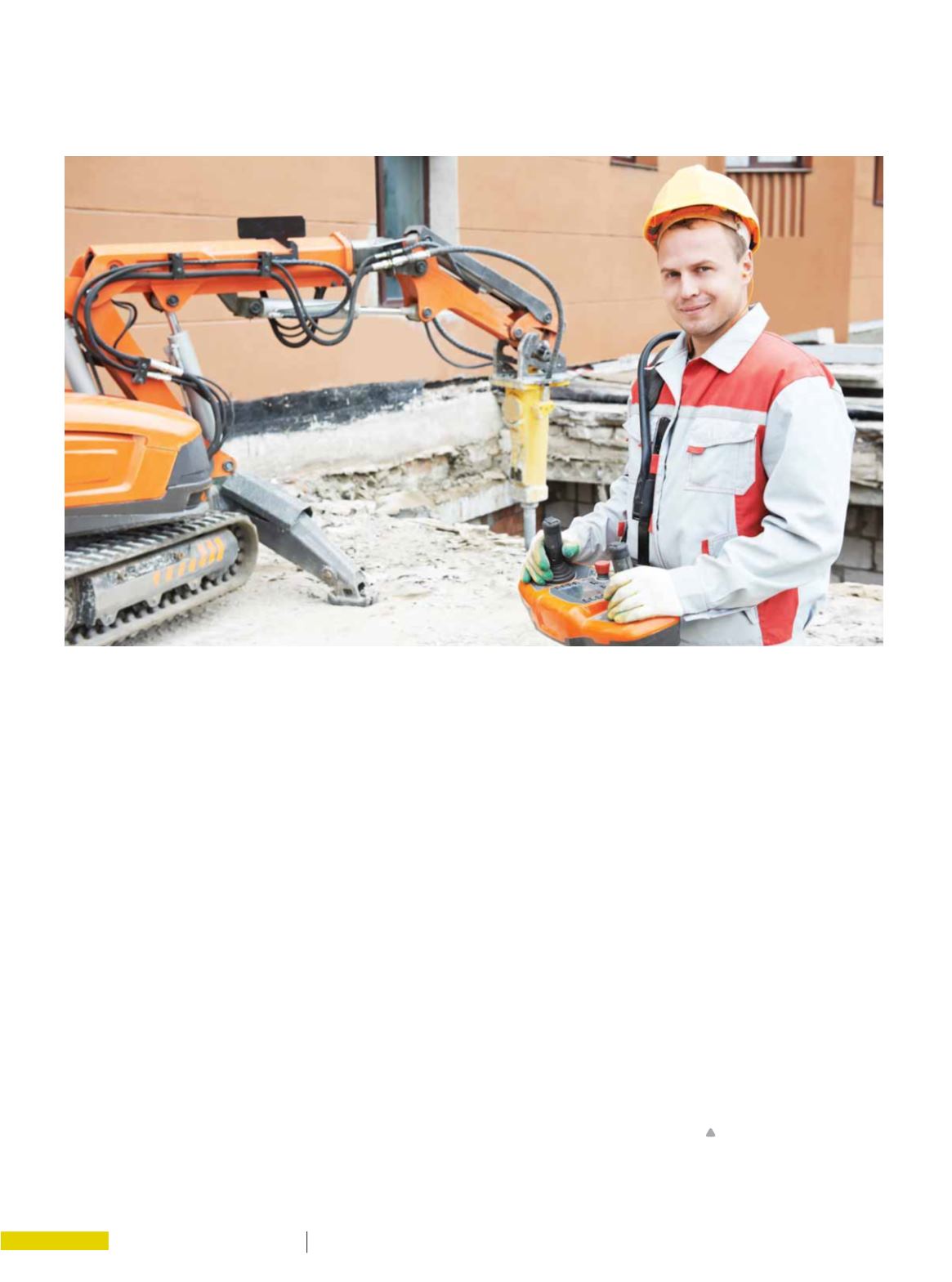
8 8
E L E C T R I C A L CO N N E C T I O N
S P R I N G 2 0 16
heavier items than they can on their own.
These are already in use in the Korean
shipbuilding industry.
Longer term, Robert thinks digital
technology combined with prefabrication
and advanced materials have the
potential to really disrupt the way we
build things.
“There is a plausible future where
many building components are
manufactured in factory conditions
with extremely advanced computer-
controlled machinery, working with very
high performing materials. This is an
industry that looks increasingly like the
automobile supply chain.”
It seems technology will inevitably
march on. But the shape it takes and
the degree to which it pervades the
construction industry largely depends
on how the industry reacts to these
new innovations. It’s not always easy to
embrace a new technology straight off
the bat, especially when it fundamentally
changes the way a certain task is done (if
it’s not broken don’t fix it, right?).
“Culture is an incredibly important
variable. In fact, we think it could be the
factor around which the whole future of
the industry pivots. Regardless of the
objective merits of a technology – how
much it can reduce risk or increase value
– if the industry doesn’t embrace it, it
will be difficult for the technology to get
any traction.
History is littered with examples
of excellent technologies that never
cracked the mainstream. When you dig
into these stories you find the reasons
are basically cultural – attitudes,
perceptions and tastes,” says Robert.
“At the same time, there is a sense in
which technology and change can happen
to us, despite our best efforts to ignore
it. Australia’s manufacturing industry
provides a cautionary example of what
can happen if we bury our heads in the
sand and hope that change will pass us
by, leaving us unscathed.”
If this is the case, our next big
challenge will be adapting training and
education models to suit. If industry
professionals are to be kept up to date
with technologies that are constantly
evolving, education will also have to be
an ongoing process. What is clear at
least, is if machines are taking care of
more of the heavy work, workers will
have more time to devote to education
and up-skilling.
“The training system we have today
won’t be suitable for a world dominated
by technology and extremely specialised
skill-sets. The construction industry
still largely relies on what is effectively
a one-shot training model – the
apprenticeship system.
This model isn’t designed for a world
where technology and products evolve
quickly and radically. Continuous
professional development is widely
accepted in many other industries but it
isn’t a part of our training system. This
will almost certainly need to change,”
says Robert.
>
Read the CSQ report at:
www.csq.org.au/farsightAs more and more processes in the construction industry become automated, job definitions and skills requirements will
invariably change.