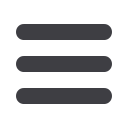
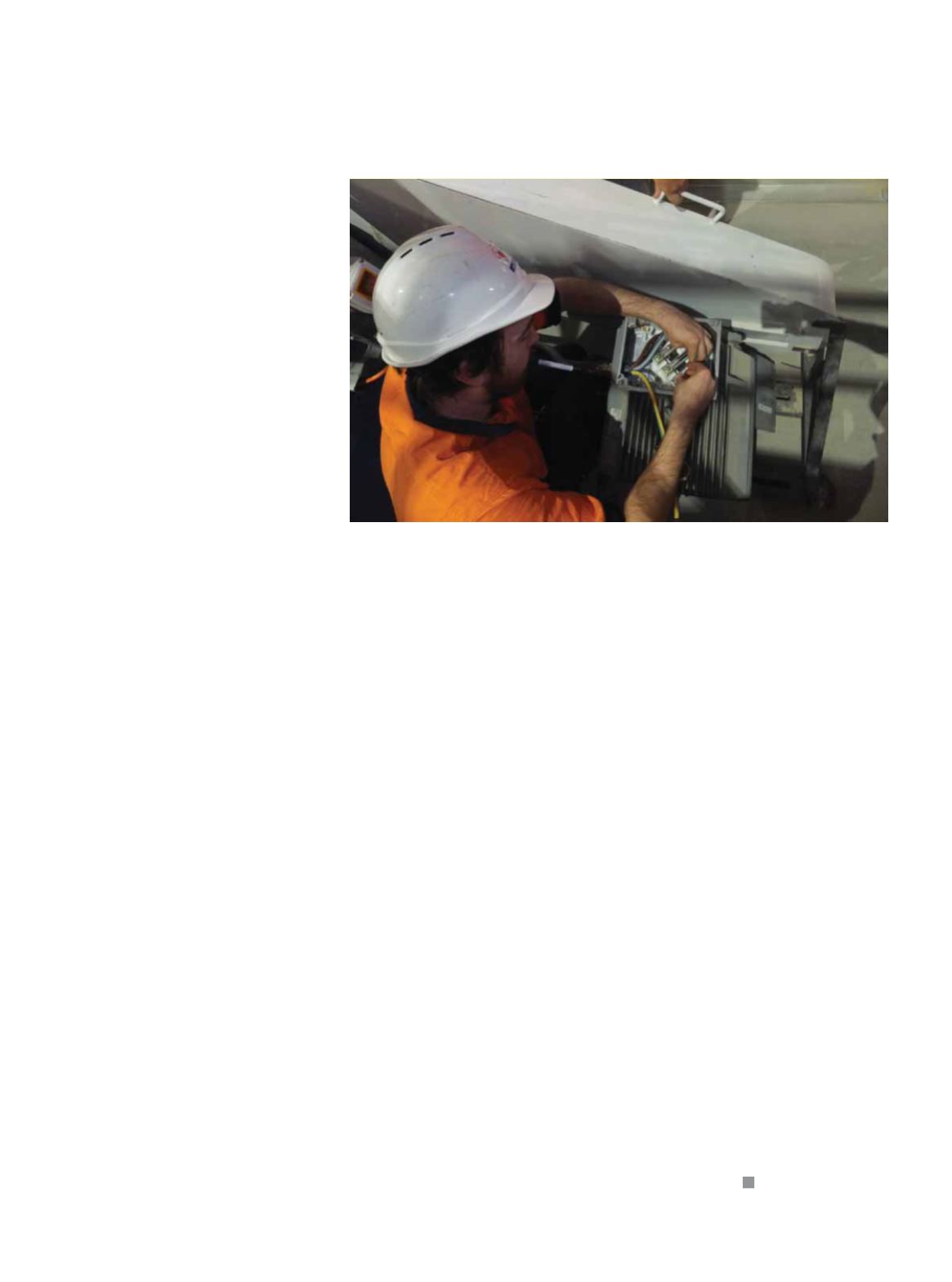
www. e l e c t r i c a l c o n n e c t i o n . c om . a u
23
finalised, the client asked Bruce to
go to India and audit the MCCs
during manufacture.
“I politely declined and said it could
all be managed through photos, Skype
calls and emails. This worked reasonably
well and ensured that the MCCs
complied with Australian fault current
requirements… sort of.”
Bruce says dealing with Indian
electrical engineers – and others with
limited knowledge of the Australian
Standards – was harder than he
originally thought.
“There was a lot wrong with these
products when I first saw them.
“First, we did all the proper
calculations and told the suppliers they
needed to upgrade all the equipment
internally to achieve fault level and
discrimination requirements to satisfy
the Australian Standards. They did
about 90%, and we had to do the rest
when the boards arrived.
“Several times we stipulated shielding
of live components – something that
was ultimately done by RIC staff on site.
“Further, the MCCs arrived with the
wrong programmable logic controllers
(PLCs) installed. Our skilled instrument
and control staff replaced them with the
specified Allen Bradley PLCs.
“Then, our in-house programmers set
up the PLCs and supervisory control and
data acquisition (SCADA) system to fully
operate the plant.”
Bruce says the suppliers did not issue
any design or engineering documentation.
“There were MCC drawings, plus some
control diagrams and PLC connection
plans. That’s all.
“This changed dramatically as the
project proceeded. We developed test
and commissioning sheets or booklets
for each MCC to ensure everything was
suitable for the site.
“These documents were designed to
help with commissioning of all motors.
They were crucial – and saved time in
that phase of the project.”
RIC Electrics was also contracted to
do all the field layouts and designs, cable
sizing and consumer mains sizing.
“Time management on this project was
a nightmare when it came to staffing.
“Indian equipment drifted in or didn’t
arrive at all. So we were requested
to take over the supply of electrical
materials for the site to ensure a timely
arrival of materials for installation and
that there were no compliance issues.
“We didn’t have the luxury of
planning. It was very much ‘design
and construct’ on the run. The project
manager had to coordinate our works
with the other contractors on site and
given the delays caused by the supply of
non-compliant equipment this created
many problems.”
In addition to sending non-compliant
MCCs, the suppliers intended to provide
paper-thin cable ladder that didn’t have
a National Electrical Manufacturers
Association (NEMA) rating.
“This meant we had to redesign all
cable ladder routes and runs to use
Australian compliant product. Cable
manufactured to Indian requirements
was inadequate, so we bought from
Australian manufacturers.
“As for the supplied switchboards, all
the internal cabling was too small and
component fault levels were incorrect.
And we had to pull out aluminium
busbar and put copper busbar in.”
The result was an intricate system
that eventually complied with
Australian Standards.
“Australian and New Zealand electrical
Standards are among the most rigorous
in the world. We can send our products
elsewhere, but people in other countries
can’t really send their equipment here.
“Dealing with international suppliers
didn’t necessarily make my job harder,
but it took a lot more time.”
Bruce says RIC Electrics had the
necessary skills to create a high-quality,
compliant electrical installation.
“Clients and procurement officers
need to understand that when
purchasing electrical equipment from
offshore, consideration of Australian
Standards is a must.
“It is not impossible to upgrade
equipment to comply with
Australian Standards but this is an
added expense.”
Everything, including the motor control centres (MCCs), had been procured from India,
which caused a lot of headaches for RIC Electrics’ staff.