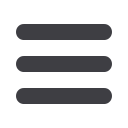
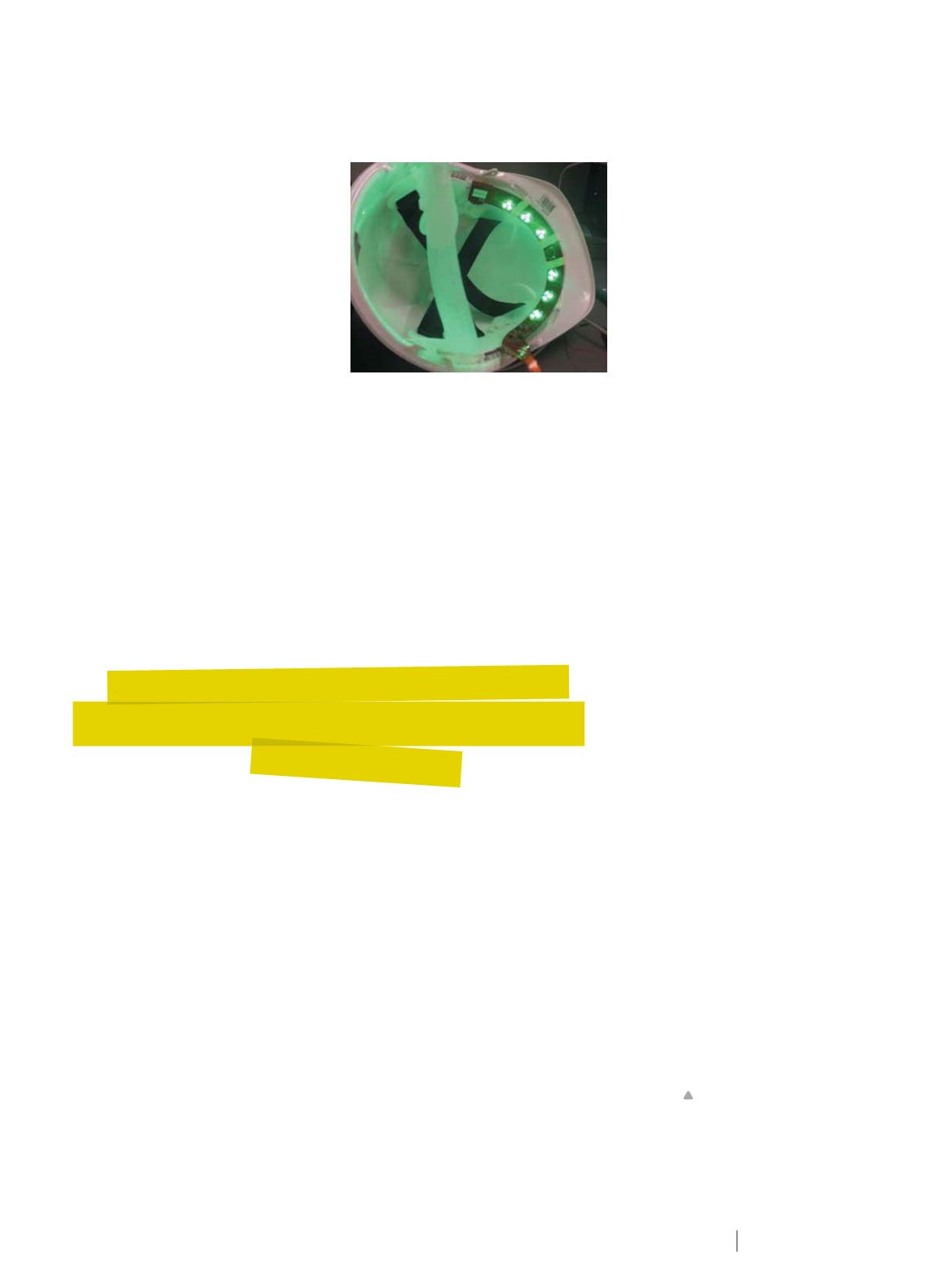
E L E C T R I C A L CO N N E C T I O N
A U T UMN 2 0 16
7 7
IWs, skilled workers will be kept better
informed and safer,” eHatsystems
founder Terry Lancaster explains.
“eHat may be the first working
example of a communication IW. It
is aimed at workers who are located
at worksites with limited access to
supervisors and experts.
“This means eHat can communicate
through the wearer’s smart phone to
an expert who is sitting at their PC at a
remote location. From the eHat camera,
the expert can see live streaming of
video and hear the eHat’s audio. The
expert is also able to send audio back to
the eHat’s headphones.”
Ultimately this means that when a
person in the field requires assistance
or has a task to be assessed, they put
on the eHat and make a call to the
appropriate expert who is registered
with the eHat system. This way the
expert can see the problem immediately
as well as communicate with the
wearer of the eHat so that the issue can
be resolved quickly or in the case of
training, a trainer can assess if the task
is being performed correctly.
The eHat itself is specifically made to
meet hardhat standards. It can also be
rated to withstand water exposure and
be able to stand high temperatures. The
great beauty of eHat is the wearer has
their hands free to work on the task and
therefore have full mobility. This is a
significant step forward in the efficiency
of communications when compared with
standard smart phone applications.
“It’s important to note that eHat is
more than just a hardhat with some
electronic gear on it. It also opens up
the opportunity for a new service,”
Terry says.
“eHat will also enable the efficient
crossing of the knowledge line. It will
enable, via its support network of
experts, the most efficient transfer of
knowledge from the people who need
answers to those who can provide them.”
When a company signs up for the eHat
service they will nominate the expert
contacts that are most relevant to their
workers; however, down the track the
company will launch its ‘assist hub’, which
enables the worker to contact the eHat
Support Centre. Through this service an
expert will be found that is the best match
to handle the equipment fault or task
required by the person wearing the eHat.
“Through the assist hub, even small
companies with limited staff can use
the resources of eHat to assist them
with situations that they are unfamiliar
with. This will have a profound effect on
how tasks are completed in the future.
Workers will need to feel they are not
left to their own devices with eHat. Real
live help will always be one call away.”
IF THE HAT FITS
eHat isn’t the only company currently
exploring smart hat technology and,
where eHat is yet to launch, international
engineering enterprise Laing O’Rourke
has been conducting field trials of its
own hardhat solution.
Developed by the company’s
Engineering Excellence Group, the smart
hardhat includes an array of sensors
in the sweatband, a GPS tracker, an
accelerometer and a data collection
unit. It has been designed to monitor the
temperature and heart rate of the wearer
working in harsh environments, plus the
external temperature and humidity.
“While the most reliable way to
measure a worker’s vital signs would be
to use a chest strap or undergarment
that is in proximity to your heart,
guys on site simply won’t wear them.
A weekend warrior out riding or
running may be happy to do that for
a couple of hours of exercise, but
making it a requirement for a full day’s
construction work isn’t feasible,” Laing
O’Rourke device engineering leader Rod
Shepherd says.
“For that reason, our system has
been designed to retrofit any hardhat,
ensuring the technology can be used
by anyone on site wearing their current
protective gear.”
In addition to the sensors there is also
a vibrating and sound alert system to
provide warning to the wearer, based
on all the data that is collected and
transmitted via a lower-power Zigbee
radio to a central gateway for storage.
The central gateway is equipped with a
3G M2M industrial router allowing for
remote access to all data collected and
can also be used to generate alerts by
SMS and email.
“We’re still in the pilot stage, but we’re
gaining a lot of insight into how to turn
this into a very robust solution that can
be used in more applications,” Rod says.
“Initially the system will be used on
projects that include high-risk activities
or extreme conditions with a view to
rolling out more broadly across the
business in the future.
“Laing O’Rourke is committed to the
continual pursuit of safety innovation
to ensure our people go home safely
everyday. This smart hardhat is just one
way we’re working to achieve that.”
With projects like these in the works,
there is hardly any doubt that IWs will
soon be a staple of any construction
worker’s toolkit. If not, I’ll gladly eat
my hat.
eHat Systems
www.ehatsystems.comLaing O’Rourke
www.laingorourke.comThe global smart hat market is
estimated to be worth $3 billion
by 2020.
Laing O’Rourke’s smart hardhat
includes an array of sensors in the
sweatband as well as a GPS tracker.