Scottish whiskey-producing region, Speyside, installs biomass combined heat and power plant
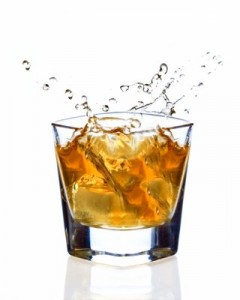
And it would appear that the region is not immune to the idea of ‘green’ electricity.
In 2009, biomass energy development company Helius Energy and The Combination of Rothes Distillers (CoRD) announced the creation of a joint venture called Helius CoRDe, which would build and operate a renewable energy scheme aimed at reducing the carbon footprint of the whisky industry on Speyside.
ADVERTISEMENT
The £50 million ($A75.5 million) project would use whisky distillery by-products to fuel a 7.2MW GreenSwitch biomass combined heat and power plant and a GreenFields plant that will turn the liquid co-product of whisky production, known as pot ale, into a concentrated organic fertiliser and an animal feed for use by local farmers.
CoRD general manager Frank Burns says: “This agreement formalises the work we have undertaken so far and sets out the structure for us to take this project forward to completion. The ability to generate renewable heat and power and secure additional markets for our distillery co-products is a very exciting development for the malt whisky industry on Speyside.”
Diageo is a global alcoholic beverages company headquartered in London, UK. It is the world’s largest producer of spirits and a major producer of beer and wine. Among others, it is responsible for the reputable Speyside whisky brands Cardhu, Cragganmore and Knockando.
Senior corporate relations manager Ian Smith explains that the idea of generating power from a distillery’s by-products has been around for several years, particularly with regards to anaerobic digestion.
“Within the distillery we have done various trials, throughout the last 20 years, so we knew that the by-products were digestible and produced biogas,” he says.
“Distilleries convert cereal starch into alcohol. The residue after distilling has high BOD. Through many trials we have proved that the distillery’s residues can be converted to biogas (about 70% methane).
“But the catalyst to actually implementing this technology and seriously invest in bioenergy had several drivers, such as the volatile nature of world energy markets; company policy to reduce our environmental footprint with regards to carbon emissions and biochemical oxygen demand (BOD); compliance with ever increasing environmental legislation; and compliance with Kyoto Protocol mechanism in particular EU-ETS Phase III, year on year declining carbon allowances.
“Further, North Sea natural gas supplies are in decline within the British sector.”
At the Cameronbridge Distillery (the largest remaining grain distillery in Scotland), spent wash (the by-product of distilling of whisky at a grain distillery) is pumped to the bioenergy facility. It is then filtered through a series of belt presses to remove the solids and the remaining liquid is then sent for anaerobic digestion.
The liquid from the anaerobic digestion process will be further treated and will be turned to steam to drive a steam turbine. The system also allows some of the water to be recovered to use in the bioenergy plant and the distillery, but only for cleaning.
Overall, the bioenergy plant will provide 95% of the distillery’s heat and power, therefore saving 56,000 tonnes of CO2 from fossil fuel. In addition, the discharge from the distillery which currently goes to the sea will have its BOD reduced by 99%.
“For Diageo, this will mean a reduction in Diageo Global CO2 emissions by 8% and BOD to the environment by 65%,” Ian says.
-
ADVERTISEMENT
-
ADVERTISEMENT