Switchboard design for a cotton gin
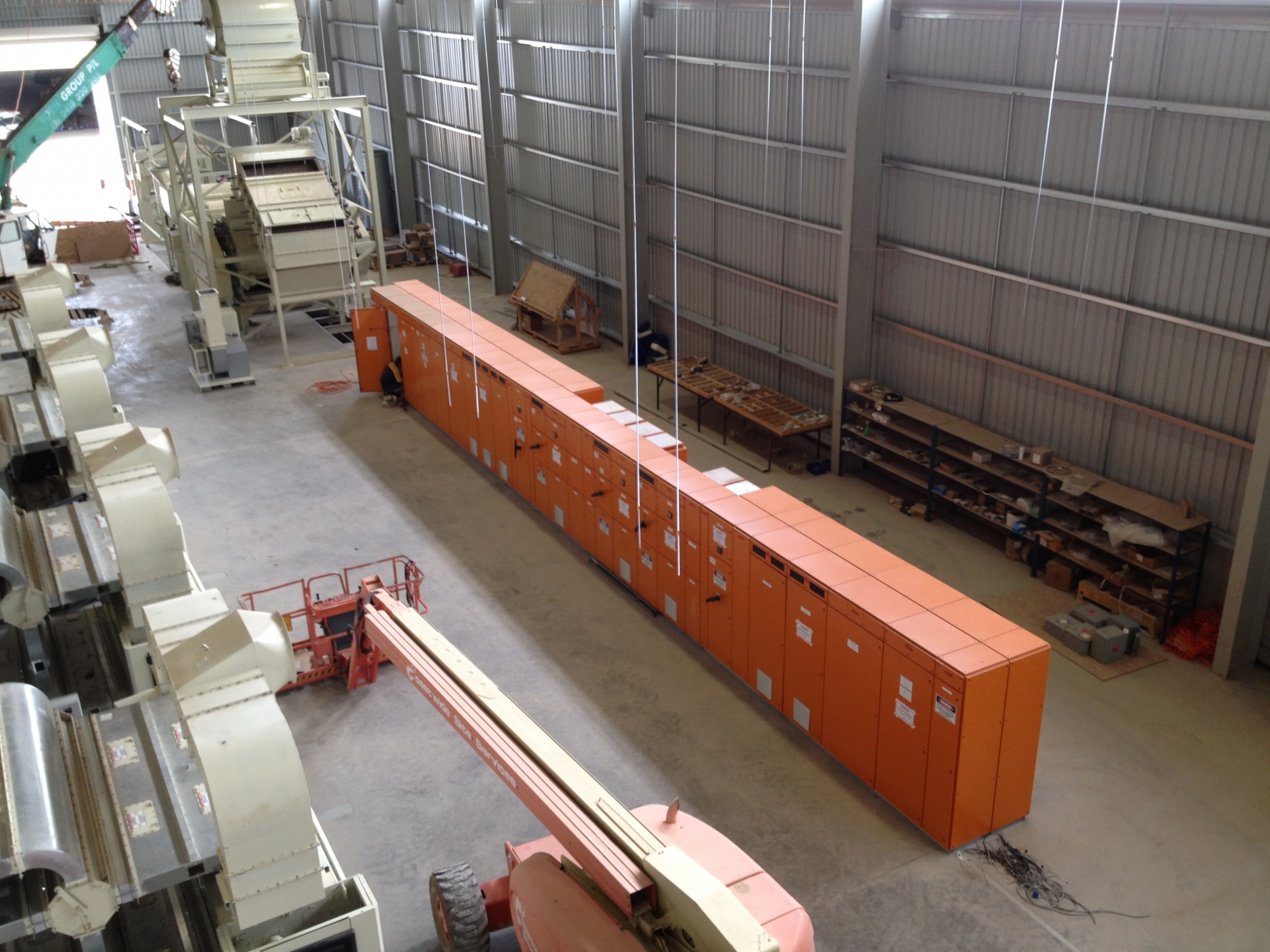
Invented by Eli Whitney in 1794, the cotton gin is one of the many inventions that arose from the American Industrial Revolution, and it’s one that completely transformed the cotton industry. Prior to its invention, the process of removing cotton fibres from their seeds required hundreds of man-hours to complete.
Simpler devices had been around for centuries, but Eli’s invention automated the seed separation process and meant that more clean cotton could be generated in significantly less time, while boosting profits for businesses.
ADVERTISEMENT
In modern times, the modest cotton gin has evolved into an incredibly sophisticated plant which uses a host of technologies to produce cotton on a larger scale and at an incredibly fast rate.
What’s more, it takes a meticulously-planned electrical installation to run it efficiently and safely.
RIC Electrics was commissioned by Southern Cotton to do just this in its gin near Whitton, NSW. The brief included the design of the main switchboard, motor control centres, distribution boards, on-site power and control cabling.
Prior information was limited – a plan which included ‘stub up’ locations and a spreadsheet of motor sizes, control cables and shaft sensors was all there was to tender from.
RIC Electrics is no stranger to the industry – the company commenced operation in 1979 in Wagga Wagga, NSW, specialising in commercial and industrial electrical contracting, switchboard design and manufacture, PLC and SCADA automation, communications and data systems, and emergency services.
However, RIC director Andrew Dwyer says this is one of the biggest projects the company has undertaken in recent times.
“Essentially, 16 weeks of work totalled more than our normal switchboard division annual turnover,” he says.
To ensure the team was as efficient as possible, the project was split into two sections: the switchboards were managed in the workshop by another director, Colin Duff, and the site installation work was overseen by Andrew.
Both of these sections had a site foreman and used over 10 different apprentices throughout the project. Most of the initial labour requirements in the workshop were carried out by existing skilled staff to cross-train both tradesmen and apprentices in the switchboard division, exposing them to a new type of experience in the industry.
Switchboards
In terms of design, three 1.5MVA substations feed the main switch board (MSB) within the gin shed which in turn supplies three separate motor control centres (MCC).
RIC designed these MCCs to incorporate a safety cut-out system for each motor. Each motor was given a safety classification into either a category one, two or three type and then a Schneider XPS safety system was installed and programmed by the team.
RIC also designed the main switchboard with a keyed bus tie system so that the three substations can be switched in and out when maintenance needs to be performed on any of the transformers, without closing down the site power.
Power monitors were also integrated so that loading on all three MCCs could be monitored.
This proved to be a crucial as energy provider Essential Energy later contacted Southern Cotton advising that there may not be enough power to run all three substations at once when other major customers are operating.
To make the design flexible, the team changed the design of one of the MCCs so that it could be easily split between two substations at a later date if required, when actual loadings were known.
Andrew says that this wasn’t the only challenge faced by the switchboard team.
“In the early stages, site works were slow as we couldn’t start until most of the other machinery and equipment was in place and the other trades had finished their installations,” he says.
“We also had to work some long hours to make sure the delivery date (which was determined by the cotton harvest date) was met, and we had to train tradesmen and apprentices in switchboard manufacture while they were on the job.
“To make things even harder, much of the equipment was being delivered from America and this was delayed several times.”
Cable trays
Because there were to be a number of ducts to be installed to transfer cotton around the gin, RIC needed to be mindful of the location of cable trays and their size.
This was done with reference to control diagrams received from overseas suppliers throughout the project.
To speed up workflow, all gland plates were laid out and punched in the workshop instead of onsite. This enabled them to be taken out of the switchboard so that they could be worked on safely and more efficiently, and saved considerable time onsite.
To prevent any future damage to cabling by any ginning machinery, strict safety measures had to be implemented.
“All the cabling in the main area was installed on cable trays, and flexible metal conduit was used from the tray to the field devices to prevent any accidents,” Andrew says.
“This meant that machinery and equipment was required to be in place beforehand so that cables could be installed in a manner which reduced or eliminated damage.”
Cable tray was also cut, bent and welded to give additional strength and aesthetic appeal.
The flood
RIC’s switchboard workshop was included in the Wagga Wagga CBD evacuation zone which complicated the project greatly. When floods hit, a late-night decision was made to raise two of the MCCs (which were still under construction) as high as possible until the danger of the flood had passed. In order to raise these, control link cables needed to be cut.
Overall, the flood cost the team two days, and additional time was then required to replace the cut link cabling.
The general site install was also affected by the flooding, with roads being cut to site resulting in 2 weeks of lost time.
Against all odds, RIC was able to deliver the project on time, with no compromise to quality, which has since led to additional work from the client.
-
ADVERTISEMENT
-
ADVERTISEMENT