How high quality wire saved time and money during Kubota Plant construction
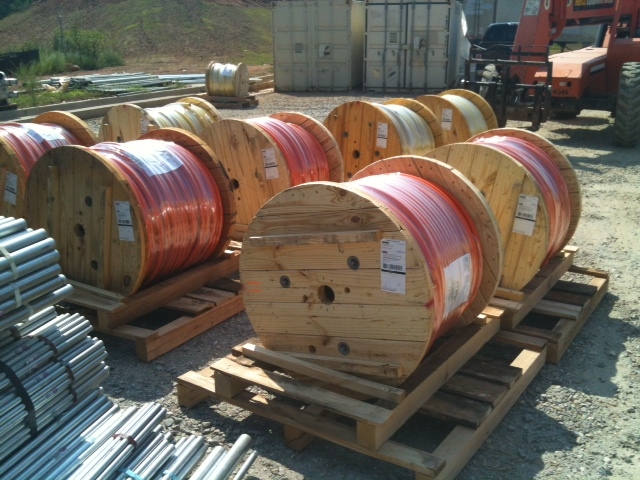
THHN cable jacketed with self-lubricating polymer reduced labour and installation costs, while a unique, sequentially printed cable reel provided accurate wire length with each cut, making it easy to plan the long cable runs required. The wire was supplied by Cerro Wire.
As the project manager for construction of Kubota Industrial Equipment’s (KIE’s) new 540,000 square foot factory in Jefferson, Georgia, electrical contractor Cedartown Electric needed wire products that would ensure the installation was fast, smooth, and trouble-free. The new facility will produce compact tractors for the North American market, and is located next to an existing 440,000 square foot KIE facility that manufactures tractor implements, including loaders and backhoes.
ADVERTISEMENT
Cedartown Electric’s project manager James Moates, who handled procurement, ordering, delivery, and installation for the facility, says, “This was a fairly decent size plant, with feeder wires that had extremely long paths, so the wire chosen had to be as easy as possible to install.”
For procuring wire, they turned to Gexpro, a subsidiary of Rexel, the largest electrical distributor in the United States. Gexpro then requested Electrical Products, Inc. (EPI), who is Cerrowire’s agent representative based in Atlanta, Georgia, to provide a quote offer for this job. EPI worked closely with Cerrowire, being sure to promote their excellent product benefits along with noting their manufacturing location nearby in Alabama.
The original specifications listed several major wire manufacturers, and EPI was successful in having Cerrowire added to the job specification as an approved product. Their addition was based on a detailed review of the specifications on the products the company had to offer.
“We were convinced that the Cerrowire products had features that made them ideal for this large installation,” says EPI’s inside sales rep assigned to Cerrowire, Carol Tinberg.
“Both Cedartown and Kubota were impressed with the wire, especially the colored wire, SLiPWire, and the true sequential footage markings and footage guarantee. They weren’t previously aware of all the benefits of Cerrowire’s products offered, and the proximity of the manufacturing plant to the job site along with EPI offering local Cerrowire stock even closer to the job site, were also positives.”
The nearness of the plant along with the large warehouse inventory provided the quick turnaround time the project managers were looking for, as well as the ability to run product to the job site within hours when needed.
Wire features on display
More than 150,000 pounds of copper wire was used on the project in a wide range of large sizes, and all colours. Many runs were as long as 800 feet and several were 1,000 feet.
Cedartown Electric attributes the ease and speed of installation to a few unique features the wire had to offer. For example, Cerrowire provided SLiPWire, a thermoplastic high heat-resistant nylon-coated (THHN) cable jacketed with a self-lubricating polymer that provides an improved, lower co-efficient of friction. SLiPWire reduces the time, labour and cost for installation, eliminates the materials and labour required for lubricating the wire, and avoids messy clean-up activities.
James Moates comments, “I found that it was a better product with the best lubricant, and just about the slickest wire I’ve seen. They were able to achieve 800 feet pulls at a rate of 3 feet a minute.”
EPI’s Carol Tinberg agreed, noting that with many other wire manufacturers you have to use additional lube, but that with SLiPWire, you do not. The product is extremely easy to install and smooth going through the conduit. On-site at the Kubota facility to observe wire pulls, EPI along with representatives from Cerrowire were exceptionally impressed with the product performance.
The contractor also appreciated the wire’s True Sequential Footage feature. A footage mark is used to document remaining wire, beginning with zero at the bottom of the reel and ending with the finished length at the top. The accurate footage mark allowed for quick identification of the re-order point, guaranteed the full purchased wire length was received, and reduced random lengths, leading to better control of end-of-reel scrap. True Sequential Footage uses Doppler lasers to ensure far more accurate precision than a mechanical counter.
“This feature made a huge difference on our job,” James says.
“Being able to do a continuous pull without reset, especially when the feeder wires had extremely long paths, made installation a lot easier and helped save money and time.”
He explained that with other wire measured by wire rollers on a spool, you often come up short on a run, whereas with the guaranteed footage, “We no longer had to guess that the wire might or might not make it on a pull. We also knew how much was left and whether we had enough left over to fill the next pull. When you’re trying to match numbers to add up to certain lengths, knowing exactly what is left on the spool makes everything a lot easier.” True Sequential Footage significantly minimized time spent with pulls, therefore helping Cedartown’s production run with exceptional efficiency.
With copper wire being as expensive as it has become, minimizing waste is an important method of saving money on a job. Using wire with the True Sequential Footage feature cut down considerably on unusable scrap wire, which has to be thrown away. This reduces inventory and minimizes labor time spent tracking wire.
-
ADVERTISEMENT
-
ADVERTISEMENT