Manufacturing, not construction – a solution to the housing crisis?
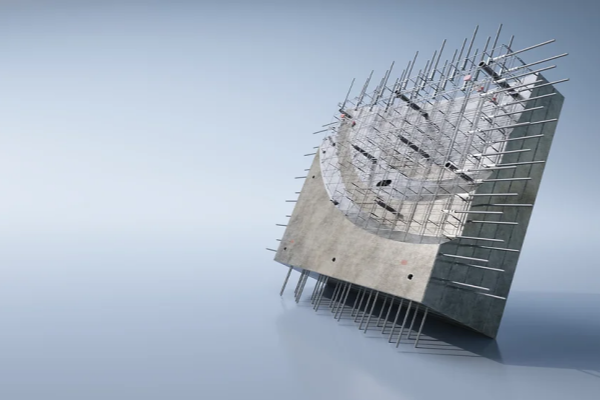
NXT Footing: This prefabricated footing is installed and secured to NXT Piling to provide rigid support to the foundations of a structure.
With still no end in sight for the housing crisis, NXT TEC. has developed a way to half the building time of homes and residential structures. San Williams finds out the method that could revolutionise the industry.
Since its onset, the solution to Australia’s housing crisis has remained relatively clear: we need to build more houses. As straightforward as this sounded, residential building hasn’t been able to catch that ever-escalating housing market.
With 4% of Australia’s total housing stock being social housing, one million public and community homes over the next 20 years have been recommended, according to the housing crisis campaign group Everybody’s Home.
ADVERTISEMENT
“The proportion of social housing in Australia has been falling off a cliff for years, all while rents, housing stress and homelessness have shot up. The private market simply won’t deliver the affordable homes that the nation requires,” Everybody’s Home spokesperson Maiy Azize says.
It’s extensive, yet necessary, especially if we’re to meet Australia’s soaring demand and growing population. Now, thanks to NXT TEC. and its revolutionary building system, this target looks more achievable.
Launched under NXT Residential, the end-to-end, rapid deployment NXT Building System can build a home at least 50% faster than traditional construction methods, with buildings assembled on site.
NXT TEC. chairman and managing director Natasha Di Ciano says the key to the system’s speed derives from its precast structure building method.
“Precast is used in the construction of commercial buildings, but nobody really knows how to make it work for the residential sector because it needed to be more cost effective and affordable. We’ve been able to do that with our advanced manufacturing,” she says.
“In Western Australia, we can’t supply housing fast enough. We were always planning on working in WA but we chose to dedicate our time to it after COVID influencing us to focus on our local economy and local housing issues.”
The precast system is made up of several patented components dubbed as “technologies” which are connected from below to above the ground. These include the piling, footing, floor system, which is the NXT Spacedeck, columns, beams, load bearing and non-load bearing or structural and non-structural walls, and mechanical joining system called casting locks.
Once the slab is laid and the superstructure is locked up, typically within ten days, before the fit-out comes in to finish the building.
“We’re not constructing, per se. Construction is not precise or predetermined and it comes with its risks. We’re not relying on someone who supplies walls and someone else who supplies floors, there’s not this disaggregated approach you find in the construction industry with building products,” Natasha says.
At full capacity, the NXT Building System can manufacture up to three houses in a day and is slated to produce thousands more homes for the affordable housing market. But there’s more to manufacturing and the NXT Building System than just its technology.
NXT Building System Technologies technical director and inventor Mataki O’Goshi Lim, the visionary who invented the NXT Building System, along with its suite of patented technologies, says knowing the “sequence” of the system is also a crucial component to making everything run together.
“When you get into the manufacturing side of things, it’s easy to do the assembly. It’s very difficult if you need a specialist to put it together. You must break down the sequence of who the team is and how you create a team to put it together. It’s important to understand everything step-by-step to the finish,” he says.
“The most important part is the structure, and it comes from not what’s just above the ground, the structure comes from what’s below. If you do not understand about the foundation built below the ground, there’s no point in talking about it above the ground.”
Mataki brings over 30 years of experience in building technology, design, architecture, engineering, manufacturing, master planning and construction management across residential and commercial projects to NXT Residential.
Having spent decades in the building industry, Mataki says too much focus is dedicated to architectural design and essentially above the ground, in addition to a lack of general gelling among building personnel, such as between the builder, architect and structural engineer.
“The industry is getting harder, more complicated and expensive. I retired in 2006 when I had enough of dealing with a lot of subcontractors damaging my material. Many people just copy, call themselves tradespeople and want to make big money with a don’t care attitude. We can’t change people, but we can influence for the better,” he explains.
The NXT Building System boasts several benefits versus traditional house construction. As mentioned earlier, the first is speed, being able to produce significantly more homes because of the process or sequence in its manufacturing.
Additionally, scheduling delay factors due to weather are also eliminated due to no on-site construction and no extra materials being ordered.
Despite the system’s building speed, NXT Residential doesn’t compromise quality. Manufacturing using concrete and steel means you’re getting an optimised building, according to Natasha, resulting in a structurally sound build, every time.
“You’re getting the best outcomes. And because we’re not wasting money on materials, we’re investing in the building the quality process, ensuring durable building structures,” she says.
Another benefit is cost saving. Because time and materials are controlled, the system allows projects to be consistently built to budget, meaning no risk of surprises or cost blowouts for their customers.
Lastly, from an environmental perspective, the NXT Building System model strives to be local, with its manufacturers and suppliers. Because it saves on logistics, it not only reduces transport costs but also reduces fuel emissions.
Overall, the NXT Residential business model has been designed around maximising and providing the utmost benefits to the users of the system. Its decentralised process enables the company to give back to the local economies in which it operates, providing more opportunities for local jobs and greater opportunities for local manufacturing.
-
ADVERTISEMENT
-
ADVERTISEMENT