Prysmian introduces flame-barrier cables
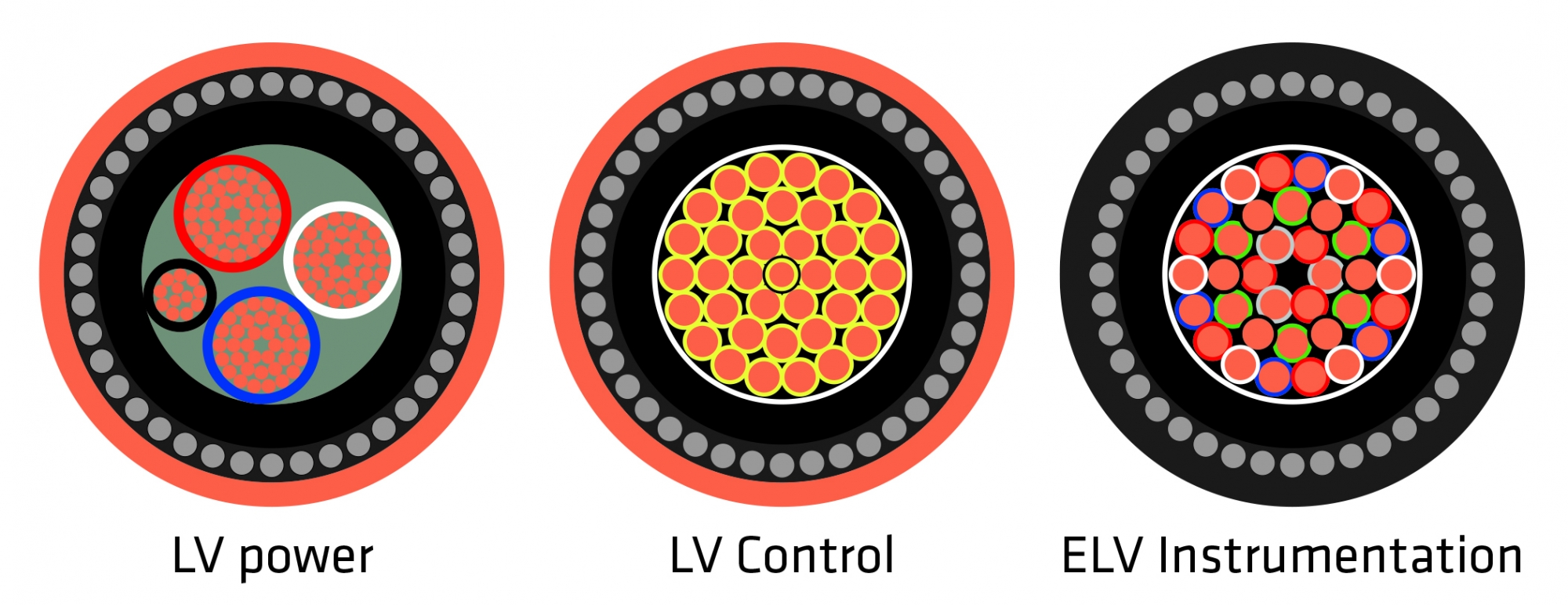
Until now, proper specification of cable systems for use in hazardous areas was an extremely complex process requiring a great deal of information beforehand, due to the fact that Australia currently has no certification scheme in place for hazardous area cables.
For cable entry systems to flameproof enclosures, the usual method was to specify barrier type flameproof glands while worrying less about the specifics of cable construction. However this added significant costs to installation due to the high cost of barrier type glands and their relatively long installation time.
ADVERTISEMENT
Prysmian has now made it simple for their clients by developing flame-barrier cables which are suitable for use with non-barrier type flameproof glands and are specifically designed to be used in a variety of hazardous and potentially explosive applications including mine sites, oil and gas platforms, fertiliser plants, chemical installations and explosive manufacturers.
Coming hot on the heels of Prysmian’s fire rated cable solutions, the flame-barrier cables are yet another example of Prysmian’s innovation and responsiveness to client needs – particularly where they relate to safety.
“We identified an opportunity in the marketplace to develop a product that would capture all the requirements for cabling in hazardous areas,” Prysmian cable design and applications manager engineering Albert Majadire says.
“The current Australian Standard merely states that such cables should be “compact and substantially circular” – naturally our design went much further, not only ensuring careful geometric arrangement of components and using fillers where required but also looking closely at all processes involved in achieving the desired geometric construction.
“We then reviewed at all relevant standards and defined an appropriate test method which involved putting our cable samples with certified cable glands and repeating the same test used to certify the glands,” Albert says.
“With our cable there was no flame transmission from the flameproof enclosure to the outside environment.
Wanting to produce cables that ticked all the boxes for their clients, Prysmian then looked at the cable requirements holistically and considered all other requirements such as mechanical performance, sheathing and reduced flame propagation.
“By meeting all these requirements in one cable and selecting enhanced performance materials to achieve the specified Australian Standard requirements, we now have cable designs that have been proven through independent testing, evaluated to the highest appropriate standards by leading NATA-accredited laboratories and which are backed by a technical report based on sound engineering practice,” Albert adds.
Prysmian’s flameproof cables cover all requirements for LV Power, LV Control and ELV Instrumentation and offer:
• Substantially compact and circular construction, evaluated and tested for gas groups IIA and IIB to the requirements of AS/NZS 60079.14-2009 clause 10.4.2 (b) and AS/NZS 60079.1-2007 clause 15.2 utilising already certified Exd rated, non-barrier type flame proof glands with sealing rings.
• Armoured cable affording wiring protection levels exceeding EPL Gb for non-energy limited wiring systems in accordance with AS/NZS 60079.14-2009 table 6. This protection level is generally adequate for Zone 1 and Zone 2.
• The option of specific engineering to provide reduced flame propagation exceeding the requirements of IEC 60332-3 category C bunched vertical test. General market orange circular TPS cables do not necessarily comply with this performance – they are required to comply only with single cable burn test to IEC 60332-1-2 which is not considered adequate performance for bunched cable systems.
-
ADVERTISEMENT
-
ADVERTISEMENT