FODC upgrades NSW coal mine communications network
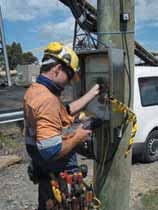
Ever since gold was found in 1851 in Ophir, NSW, Australia has been a nation of miners. Today, the mining industry is reportedly responsible for employing 2.2% of the national workforce.
But mine sites can be dangerous places for workers, so operators spend a lot of time and money frequently upgrading safety equipment, in particular the communications system above and below ground.
ADVERTISEMENT
Recently, Wollongong-based communications contractor Fibre Optics Design and Construct (FODC) overhauled communications at Vale Australia’s Integra coal mine in Singleton, NSW.
“We completely upgraded the fibre optic network – from the open cut to the underground work areas,” general manager Michael McKeogh says.
“It was a complete revamp of the entire communications network.”
FODC was founded in July 2005 and since then has experienced rapid growth, driven by high-profile projects including the Sydney Harbour Bridge communications upgrade, installation of the fibre optic communications network for Sydney’s Lane Cove Tunnel, exchange wiring for Telstra’s Next G project, and the design and installation of the communications networks at several Illawarra and Hunter Valley mines.
For the Integra coal mine project, FODC was responsible for rolling out 8km of cable underground in a harsh mining environment and 3.5km of above-ground cable over incredibly rough terrain.
In November 2012, the project won the voice/data category at the 2012 NECA National Excellence Awards.
Commencing in August 2010, FODC worked with the mine’s operator to design a novel solution involving four installation methods. The project was finished within the deadline and greatly increased the efficiency of communications. It also cut costs for the site operator.
The underground component of the project required careful planning, as the existing network was frequently damaged by underground mining machinery, causing expensive outages.
The cable route and installation method had to be carefully assessed early in the process. Steel-armoured fibre optic cables were used because of the harsh environment and the need for protection against rodents. Where cable had to be run through existing mining infrastructure, steel-armoured composite cable was also used.
“Communications in a coal mine are always problematic,” Michael says. “One of the systems connected to the fibre optic backbone was for wireless communications. This is used for portable phones and radios, and as a tracking system.
“It’s a difficult environment for a wireless system to work, because soft rock such as coal absorbs wireless signals. To get around this we had to install a lot of antennas and aggregation points.
“The resultant system means miners can now use portable telephones while they are underground, which is great for safety.”
For the aerial component of the installation, the harsh environment and technical challenges of the project required a particularly inventive approach. At least 20 designs were developed before the project could be built. In the end, aerial conductors were used in many locations.
However, due to the height of the mining machinery, aerial conductors could not be used around existing infrastructure and overland conveyors. On existing power poles, all dielectric selfsupporting (ADSS) fibre optic cables were used. So, how does the technology hold up in a mining environment?
“When it’s done properly, it holds up very well,” Michael says.
“The enclosures we used were all extra heavy-duty stainless steel, rated to IP67, so no dust would get in. Mines are very dusty, windy environments.
“Underground, we used a series of steelarmoured composite cables. We also installed some military-grade composite fibre and copper cable, and we’re the only ones in the world using it. It offers a ruggedised OS2 fibre solution, which means it’s bend insensitive – you can bend it far tighter than the usual fibre and it will still operate.
“The challenge is in the installation – specifically fusion splicing. You couldn’t take a fusion splicer into a worse environment.
“One day I took a brand new splicer into another coal mine. They insisted I did the splicing in what they call a ‘travel road’, which is one of the busiest sections of the mine. After a single 24-fibre cable, I had to throw the splicer away. It was destroyed – a $20,000 machine!”
Michael says that compared with office fitouts, the greatest difference is safety.
“Safety is the biggest consideration when working in a mine. The equipment we use to join and test the fibres can create their own hazards if used in the wrong location. There are many areas in mines that can have hazardous gasses in addition to other serious hazards just by being in an underground environment.”
An estimated 20% of the project was taken up by risk analysis and safety briefings.
“When it came time to install the overhead cables above ground at Integra, we had to work around trucks that weighed up to 200 tonnes and were 23m tall.
“We had to install 3.5km of aerial cable while the mine was active, while still being efficient and not interfering with the safe operation of the mine.”
Overall, the successful completion of this project represented a big step forward in safety and efficiency for the Integra coal mine.
-
ADVERTISEMENT
-
ADVERTISEMENT