Phoenix Contact Crimphandy – a mobile stripping and crimping tool
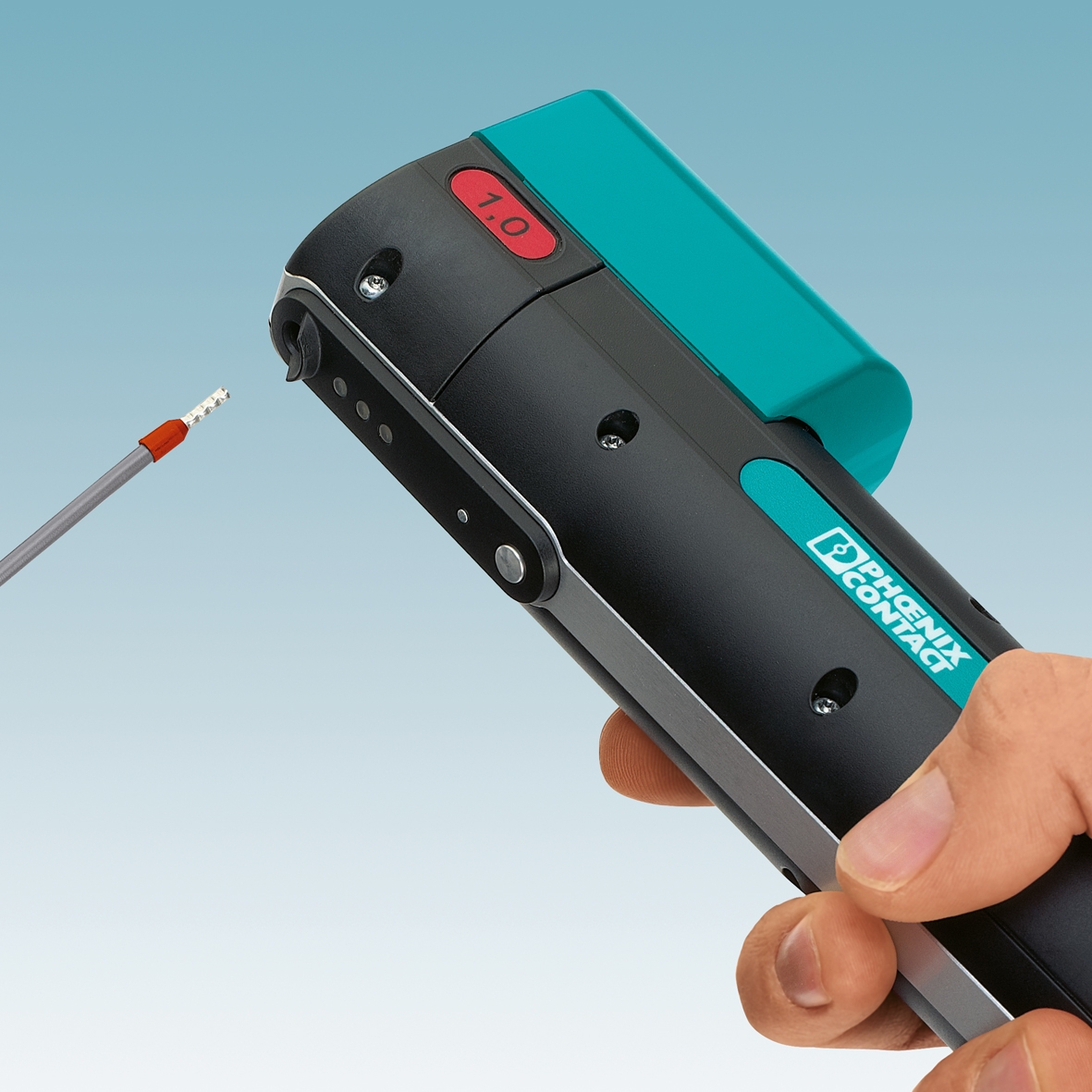
A crimped connection is a connection between two components that cannot be released, meaning it provides a reliable, long-term electrical and mechanical link. The connection between the two components is extensively specified and can be tested according to standards such as DIN EN 60352-2. The standard’s value tables specify the extraction forces that each conductor needs to be tested for. For testing of the end sleeves, DIN EN 60999-1 applies.
Users demand reliable tools
ADVERTISEMENT
Whether a connection ends up being secure and reliable depends largely on the tool choice, but also on whether the crimping is performed manually or by machine. Phoenix Contact offers solutions for both approaches. Users would prefer not to have to test their crimped connections; they would rather be using tools that produce reliable results in the first place. However, the market requirements – fast, compact, highly reliable wiring – can be very challenging, particularly when it comes to small to medium-size control cabinets. For this work, users need to have a reliable product partner who not only provides the most suitable tools but also helps to optimise the installation process. Many users do not realise how much they stand to gain in switching from manual to powered crimping tools.
Manual crimping pliers are flexible and portable
Here is the process for putting an end sleeve on a conductor: First, the conductor is stripped using the crimping pliers. This is where the first visual checks need to happen. Is the conductor stripped properly? Are any of the wire strands damaged or truncated? Was the insulation layer cut cleanly and removed properly? Or are there ‘bite marks’ on the insulation? Next, the end sleeve is placed on the conductor, ensuring that none of the wire strands are missed.
After that, the conductor is usually twisted slightly so that none of the strands stick out. Ideally, this slight twist would not be needed, as the wire itself is already twisted underneath the insulation. Additional twisting in the wrong direction may undo the original twist and thereby achieve the opposite effect – loosening all the strands. Additional twisting in the same direction, on the other hand, can widen the conductor diameter, which may prevent the connector from fitting over the conductor. If additional twisting is absolutely necessary, it should never be done in the opposite direction to the conductor’s existing twist. In any case, the diameter of the twisted strands needs to be smaller than the diameter of the external insulation. Next, the end sleeve placed on the conductor needs to be crimped down. This requires a tool that exactly fits the conductor cross section. Some crimping pliers have an adaptable swage, whereas others have a swage with multiple crimp nests to match common conductor cross sections.
An experienced user will take around ten seconds to complete the crimping. If there are a large number of contacts to be crimped, this may entail a considerable amount of human error. Manual crimping tools definitely have their own advantages – they are flexible and highly portable. However, in terms of time consumption and error potential, they are of limited use in heavy-duty work.
Powered tools for speed
The other option is to use powered tools: Powered stripping tools, powered crimping tools, or a combination of the two. The tool is powered either electrically or by compressed air, or both. Looking at stripping and crimping as part of the same process, it makes sense to use a combined tool for the two tasks. Powered tools like this do not have dies that automatically adapt to the different conductor cross sections. The user needs to select the most suitable stripping die for the cross section to be stripped. The crimping swage, on the other hand, usually covers a range of cross sections, which means that the same swage can be used for crimpings ranging from 0.34 to 2.5 mm². The swage would only need to be changed if there were any cross sections larger than that.
The work cycle of such a power tool – e.g., one of Phoenix Contact’s Toolfox models – is a lean 1.2 seconds; this is all it takes to strip the conductor and crimp an end sleeve onto it. That makes the powered tool approx. ten times faster than the manual tool. Also, there is no need to check the conductor or to twist it. As a result, the user not only takes less time but also is less likely to perform inferior workmanship. At a weight of around 10kg, such a powered stripping and crimping tool is mobile, but it does require a fixed power or compressed-air supply.
Crimphandy – the best of both worlds
What users need is a device that combines the flexibility of the manual crimping pliers with the speed and reliability of the power tool. Enter Phoenix Contact’s new Crimphandy – the world’s first mobile powered stripping and crimping tool to be released on the market. Due to its low weight and cordless nature – no need for power leads or compressed-air hoses – the Crimphandy is extremely mobile and can be used directly inside the control cabinet.
This new tool takes a mere two seconds for stripping and crimping. Reproducible crimping directly inside the control cabinet is made possible through battery power (Fig. 1). Because the Crimphandy has a built-in storage magazine for the end sleeves, there is no need for cartridges or any other accessories. Three differently colored LEDs are provided to indicate the device status, including magazine and battery levels. The Crimphandy is suitable for control cabinet assembly, machine engineering, interior installation, and any other areas that involve working with conductors (Fig. 2). The device is roughly the same size as one of Phoenix Contact’s cordless powered screwdrivers. The Crimphandy is aimed directly at the given market requirements – to provide more efficiency without sacrificing any of the manual flexibility (Fig. 3).
Excellent integration with push-in terminal blocks
Market demand for ever faster and more compact wiring extends to more than just the tools used to construct the control cabinet. The terminal block concept also needs to follow suit. This is another area where the Crimphandy can show off its efficiency. The push-in terminal blocks from Phoenix Contact’s Clipline complete product range are known to be some of the most efficient terminal blocks available today: The conductor is stripped, an end sleeve is clamped on, and it is plugged in. No tools whatsoever are needed for connecting to the terminal block. Similarly, the conductor can be released without the need for any specialist tools. The PT product range features an integrated push button. When this is depressed using a standard screwdriver, the contact opens and the conductor is released. Thanks to the new Crimphandy device, the step that precedes the connection can also be made more efficient. Regardless of where the control cabinet is located, the Crimphandy can always be taken along. The conductor is prepared on the spot and then inserted into the terminal block – all of which takes less than five seconds.
-
ADVERTISEMENT
-
ADVERTISEMENT