The sound of R&D at Schneider Electric
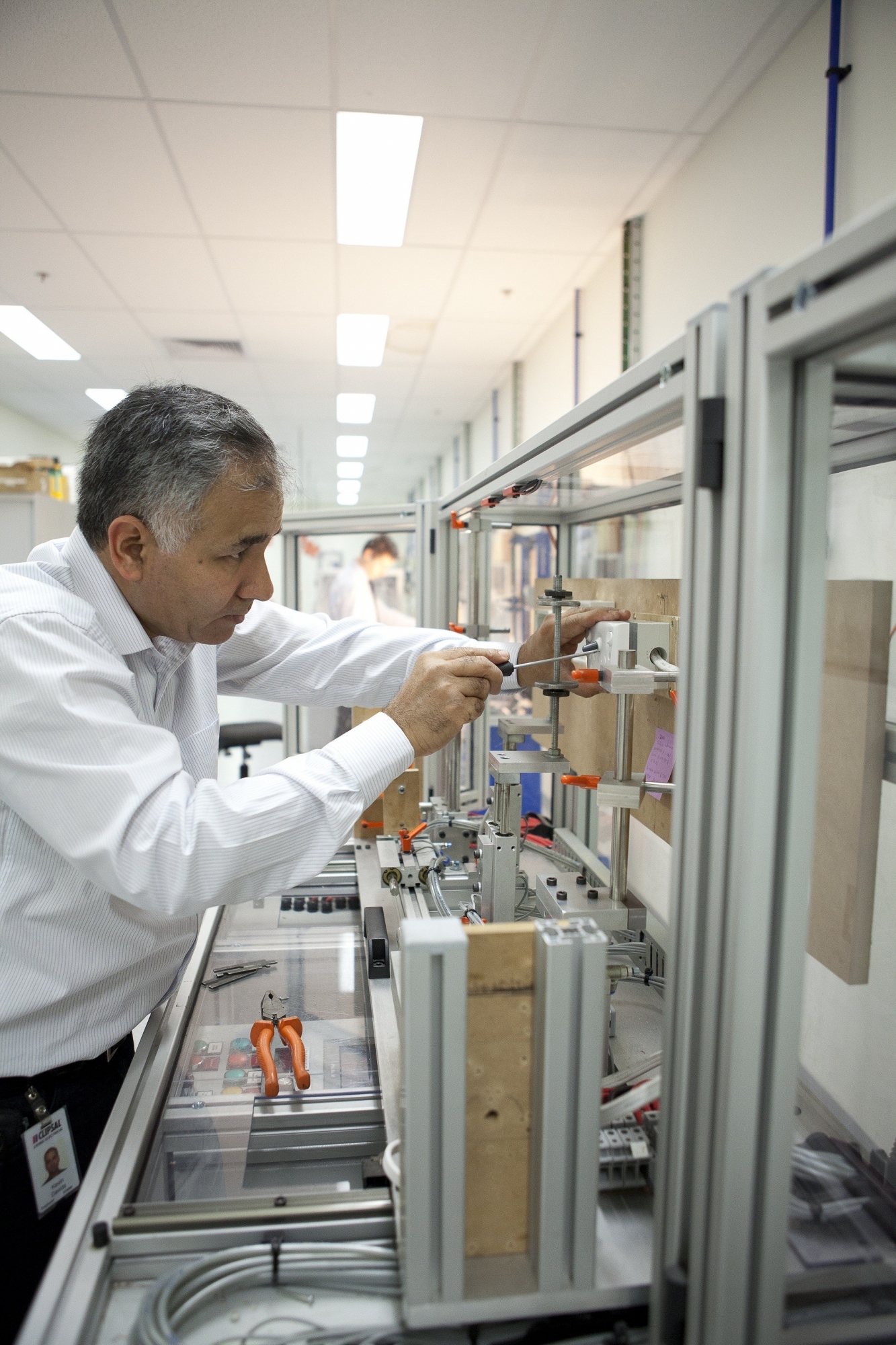
The company invests around $20 million dollars each year in research and development of new products at the Gepps Cross site in South Australia where Clipsal branded products are manufactured. An integral part of this investment is testing to ensure Clipsal products are among the highest quality and most durable on the market.
A rhythmic hum can be heard coming from the Schneider Electric Research & Development (R&D) labs at Gepps Cross – it’s the sound of new products being rigorously tested before they are released onto the market.
ADVERTISEMENT
Sometimes running 24/7, the testing apparatuses here have been configured to push and pull plugs in and out of sockets, to mimic extreme environmental conditions and to test the durability of a product by repeatedly dropping it from height.
Many hundreds of electrical contractors and builders visit the R&D labs throughout the year. The tour begins in the development workshop where engineering drawings are turned into 3-D models.
“Anything that can be created on our CAD System can be built in our workshop in conjunction with our Rapid Prototyping (RP) machines,” says Clipsal by Schneider Electric’s development technician Allan Brown.
“Using Fused Deposition Modelling (FDM) technology we build prototypes of products so the engineers can better see and feel how the new design will work.”
Unlike conventional machines which remove material to produce a model, the RP machines, using an ABS style plastic, build up models to functional prototypes – something like a complex 3D photocopier. For a typical switch surround the build time is hours, compared to days using conventional machining methods.
A testing scenario
In the main R&D labs, Clipsal by Schneider Electric test engineers run products through a variety of testing apparatuses to ensure they are performing to the highest standards, often facing more rigorous testing than what is officially required.
“The Australian Standards require that a 10A switch be operated 12,000 cycles,” says Clipsal by Schneider Electric test laboratory leader Tuan Nguyen.
“Our internal requirements call for the product to be tested 1.5 times electrically and 3 times mechanically – i.e. the product must pass 18,000 operating cycles at full load and a further 18,000 operating cycles at no load, totaling 36,000 operating cycles.”
One tester apparatus is able to carry out up to six tests simultaneously, testing different products all at once. This saves time and money in getting the finished product to the market faster. Products are also tested at high voltages; with everyday corrosive substances; and in high temperatures to see how they perform.
“This is a very flexible space,” Clipsal by Schneider Electric testing engineer Martin Mielczavek says of the lab area.
“Here, we can set the machines to test whatever specific action we require. Whether it be turning switches on and off a number of times, or looking at the force required to push in a plug.”
Environmental chambers in the area create artificial environments of between -30 degrees centigrade and up to 90 degrees centigrade, with the option of between 10% – 98% humidity. The products are used in these conditions, and then tested to ensure their continued reliability.
In the temperature rise room, which is kept at a constant temperature (usually around 25 degrees centigrade), the products are installed and a rated current is allowed to pass through the contacts of the product(s). The current ranges from 10A to over 100A. This high current causes the contacts to heat up. If the products are not designed properly, then this heat buildup can cause the products to melt or catch fire, causing a safety risk.
Standards specify the maximum temperature on the various parts and the Clipsal By Schneider Electric test engineers ensure the products do not exceed the limits. Another room houses testing facilities for Clipsal’s ceiling fan range. Air flow, noise level and stability are all measured.
“We run most of these tests on any product that we develop here,” Martin says.
“The products are developed and then tested to ensure that what we put out to market is of a very high standard. If for some reason it does not work when we test it, then we fix it and test again.”
Dean Partridge of DP Electrical Services in Melbourne recently took part in a tour of the R&D labs.
“It is an amazing facility here,” Dean says.
“I didn’t realise the extent of the testing that was done. I have always been loyal to the brand, and I know from experience the quality of the product, but to see all the work that goes into bringing a product to market is something else.”
Riaz Rezvani, a builder from Sunland Homes, which operates in Queensland, New South Wales and Victoria, also thought the tour was very insightful.
“It was definitely an eye-opener to see the extent of the Clipsal by Schneider Electric operations,” Riza says.
“It is good to know the products are so thoroughly tested.”
Schneider Electric is committed to developing and manufacturing quality Clipsal products that comply with Australian Electrical Safety Standards. As well as in-house testing, the products are independently tested by specialist, third-party accreditation laboratories in order to meet specific product application standards.
When Clipsal products are upgraded, or improved through design or performance, Clipsal will reapply for independent testing and approvals to ensure products continually meet Australian standards.
Quick facts:
• Clipsal invests around $20 million dollars each year into research and development.
• R&D employees at Gepps Cross are part of Schneider Electric’s 11,000 R&D global network.
• 4.9% of Schneider Electric’s turnover invested in R&D globally.
• Clipsal employs a highly trained team of engineers in design, development and testing.
• Clipsal engineers travel the world, particularly to Europe, in search of the best equipment and manufacturing techniques to provide the market with the most advanced, ‘state of the art’ electrical solutions.
• Innovation comes from a sound knowledge of markets and applications, with a strong focus and involvement with customers in the design process.
Site tours are regularly organised throughout the year. If you are an electrical contractor and would like to visit, please contact your Clipsal by Schneider Electric Sales Representative who can coordinate a tour.
-
ADVERTISEMENT
-
ADVERTISEMENT