Audits discover major problems with solar panel installations
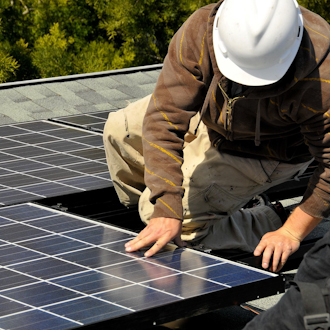
The recent findings of faults in solar systems by inspectors in New South Wales appear to point to the lack of a uniform code of installation practice in Australia.
Notwithstanding Australian Standards, and the rules applied by the Clean Energy Council (CEC), it might be difficult to satisfy a particular inspector on a given day. There is (as always) the problem of interpretation, but there are also occasions when the rules are confusing.
ADVERTISEMENT
One example is the apparent requirement to have DC isolators mounted at the panel as well as at the inverter input, and a second one is the replacement of DC circuit breakers by isolators. There are also requirements which do not appear to have much basis, such as the time-out needed for an inverter before connecting to the grid. Then there’s a question that arises as to why a DC breaker is not suitable as an isolator.
In order for a client to get his or her REC credits, the solar installation has to be installed by a CEC-certified electrician. That would, you’d think, provide an approved installation in all respects. However in some cases, the person actually doing the work is not CEC-licensed, and once the installation is completed an accredited electrician signs off.
The lack of clarity in requirements for solar installations makes it difficult to judge how serious the NSW inspection results are (20% of installations were deemed dangerous and 60% had less than serious deficiencies).
Solar installations, being exposed to weather, require wiring and components that will stand up to stressful environments. Wiring, we believe, ideally needs to be double insulated but this is not necessarily the case in many installations. Thermoplastic cable (as used in AC house wiring) is not suitable and not being double insulated, requires to be run in conduit. The connectors used must also answer to requirements that are more stringent than for the equivalent AC currents – arcing being a major problem. This is also the case for DC circuit breakers.
The use of polarised circuit breakers also poses a potential hazard. If incorrectly installed – and that is easy to do – the results can be disastrous (electrocution and house fires). Generally double pole breakers have to be installed and great care needs to be taken with polarity markings on the devices selected. Some are marked with polarity symbols at the bottom; some have polarity markings at the top and others at both top and bottom.
This article is not intended to serve as an instruction manual; however, this cautionary note is of use: it is the polarity of the PV panel array (not the DC input terminals of the inverter) that determines the connection. Because of the possibility of ‘getting it wrong’, some State and Territory regulations require the use of unpolarised isolation and/or circuit breakers. It is also important to carefully read the relevant Australian Standard (AS/NZS 5033.2005).
Excessive leakage current to ground will cause some inverters to shut down. DC insulation resistance has to be higher than for house wiring because high DC voltages are used. However parasitic capacitance of the panels is likely to be the major contributor of leakage current. This also depends on the inverter chosen as some have significant AC ripple on the DC rails.
Inverters
Inverters come in ratings from about 1.5kW upwards and for domestic installations generally do not go higher than 5kW. The larger ratings are mainly of European origin whereas the smaller ratings are almost exclusively manufactured in China. It is difficult to comment on design and quality issues although many of the products appear to be well constructed even if the accompanying documentation is often brief to the point of lacking important technical information.
Problems with inverters can be classified as inherent ones including design aspects, and inappropriate applications, as well as those occuring because of incorrect installation procedures. Electrical Connection makes no claim as to being able to comment on design aspects. There are special trade magazines that thoroughly test solar inverters, and in particular how they stack up against published specifications. These should be consulted by systems integrators, one critical item being the ability of the inverter to fully utilise the available power from the PV panels.
As an example, a 3kW inverter may in fact only peak at 2.8kW. Obviously a solar system provider needs to know ahead of time that there is a deficit so that a higher rating inverter can be chosen to match PV panel capacity.
Inappropriate installations include poorly selected PV panels that are not matched to the inverter capacity. Panel selection is not rocket science but neither is it a matter of ‘back of the envelope’ calculations (we have been told of inverters on which a calculation of panels required can be seen scrawled with a marker pen on the inverter housing). Incorrect installations include examples – hard to believe unless you see the results with your own eyes – where the DC input plug to the inverter has been removed leaving a largish hole through which the DC wiring is introduced to the inverter’s internal circuitry. The weatherproof rating is thus destroyed!
In another example, a large access hole had been cut into the housing, leaving you to wonder about metal debris thus nicely distributed over the printed circuit board. We saw one example where the inverter’s input DC plug had been partially destroyed so that the special tool required to unplug the PV panels would not have to be used (obviously the use of a special tool is a safety measure to prevent unauthorised access to dangerous DC voltages). This is evidence of unprofessional practice and as such the findings of the NSW Government’s authorised inspection of solar installations come as no surprise.
There are also faults that really require investigation but the paucity of technical information available for many of the smaller rating inverters makes this a tough task. One problem is the effective ‘frying’ of an inverter with a possible cause being a voltage impulse having taken power components. Our question on whether Metal Oxide Varistors (MOVs) were fitted drew a shrug.
Other problems appear to be evident in control circuitry, one being the shutdown of the system when the maximum input power was being exceeded (it seems logical that power would be cut back to the level of the maximum rating), and others relating to Radio Frequency Interference (RFI). Radio reception of signals in the AM band can be badly affected.
So what constitutes a good installation?
Despite the apparent confusion in ‘blogland’ as to many requirements, the Australian Standards (AS/NZS 5033) are reasonably specific. For example: polarised DC breakers are not allowed to be used to isolate and/or protect individual sub arrays (the reason: they can be subjected to current reversal) notwithstanding the fitting of blocking diodes – these being optional as is the fitting of bypass diodes on individual cells or strings.
DC breakers are allowed provided they are also rated as isolators. Alternatively isolators and fuse combinations may be used provided the fuses are rated for DC. Small arrays comprising of five or less strings do not require an array isolator. Polarised circuit breaker/isolators are permitted on the inverter input.
Earthing is, on the other hand, less specific. Systems may be isolated on the DC side with the only earthing point being the AC output (i.e.: grid connection point) via the neutral bar-earth bar, or they may be centre-earthed (i.e.: a DC system earth in the centre of two array structures), or have only an equipment earth, meaning that exposed metal of the PV installation is earthed (note that this may be very necessary in areas of high lightning activity). Transformerless systems may not be earthed on the DC side.
Some inverters are equipped with earth leakage monitoring using a resistance to earth measurement circuit. System-earthed solar panels, we believe, should carry an earth leakage breaker. These may be fitted at the DC terminals of the inverter.
What the installers tell us
So-called solar specialists make all sorts of guarantees but does the consumer get what he or she is being told? In Victoria, Energy Safe Victoria looks after safety and inspection after installation, but what about in five, 10 or 25 years? Is there anything being checked to ensure that the system meets the energy specifications over time?
In the majority of cases a consumer will not have had contact with the installers or accredited designers. The duty of care is apparently thrown back to the consumer. CEC states on page 27: “You should think carefully before selecting a designer/installer. Online and mail-order solar PV system suppliers who never visit your home may have difficulty recommending the most appropriate equipment.”
There are instances where inspectors have refused to go on the roof because they have no OH&S insurance coverage, instead using binoculars to view the installation from ‘across the road’. Systems are sold on price alone, and it seems corners are cut using low-quality components.
Solar PV systems, not the province for the inexperienced
Solar PV installations require expertise distinctly different from that for AC house wiring. There is need for documentation for installations as well as signage and labelling of control components such as DC isolators. In Victoria the Electrical Telecommunications and Renewable Energy Contractors (ETREC) Association provides appropriate training for installers, all of whom need to be licensed electricians in order to participate in the training programs and must have Occupational Management Plans in place before being endorsed by the Association. Tradesmen who wish to acquire expertise are advised to contact the Clean Energy Council (CEC) for authorised training establishments in their State or Territory.
-
ADVERTISEMENT
-
ADVERTISEMENT